Die DNA des Stahls
Stahl-Entwicklung 4.0. In einer Forschungskooperation entschlüsselt der Grobblechhersteller Dillinger Geheimnisse des Stahlgefüges.
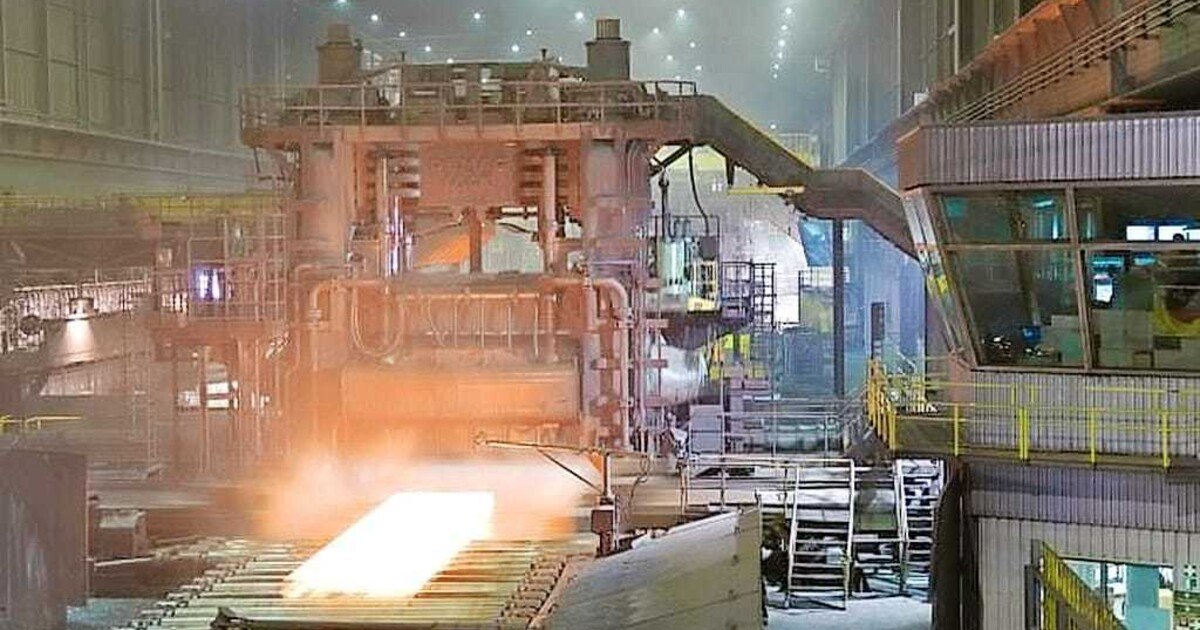
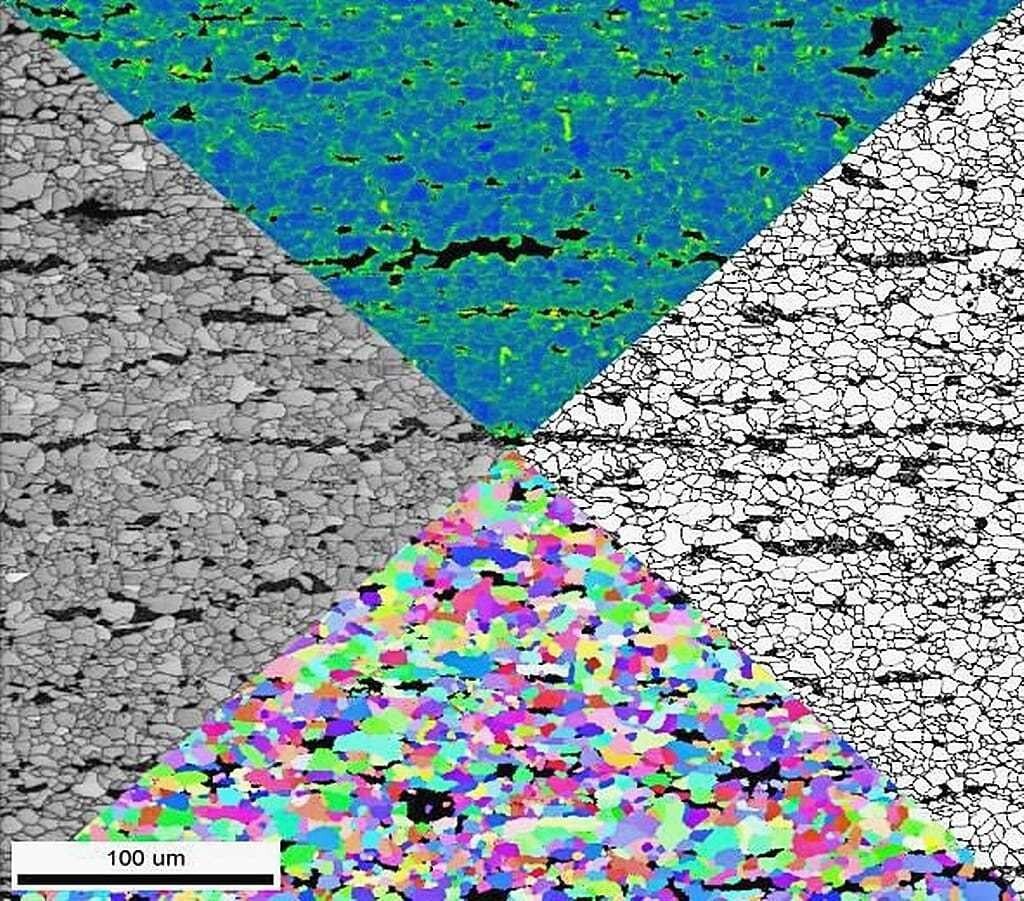
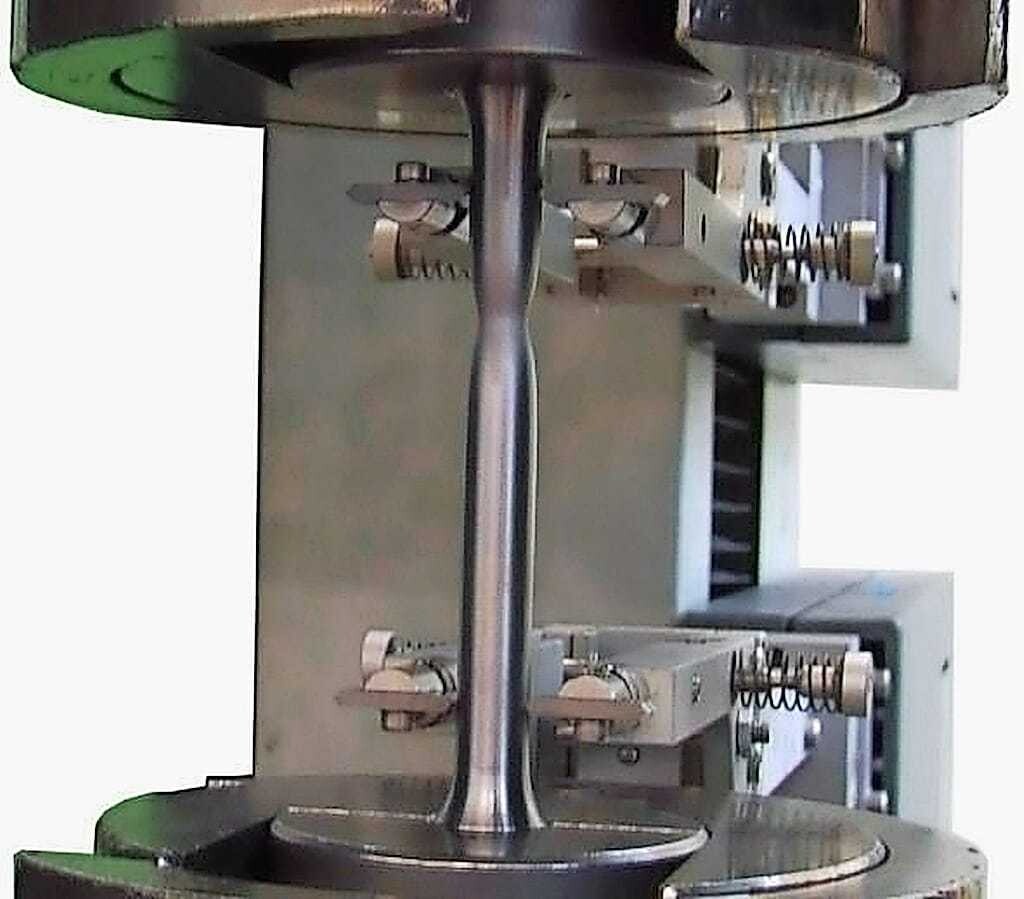
Mit einer integrierten Forschungskooperation fördert Europas führender Grobblechhersteller, Dillinger, die Erforschung der Mikrostruktur von Spezialstählen. Neu entwickelte, ausgeklügelte Analysetechniken und Simulationsverfahren erlauben den Blick in bislang unbekannte Tiefen des Stahlgefüges und auf die für seine Bildung entscheidenden Einflüsse im Produktionsprozess. Das angestrebte Ergebnis ist ein neues Verständnis der Zusammenhänge und damit die Möglichkeit, die Realisierung immer anspruchsvollerer Eigenschaftsprofile extrem belasteter Stähle präzise vorherzusagen und anschließend in die industrielle Fertigung umzusetzen.
Höchstleistungs-Werkstoff
In Fundamenten und Plattformen von Offshore-Anlagen müssen Grobbleche jahrzehntelang Höchstleistung vollbringen. Extreme Einsatzbedingungen wie arktische Temperaturen, hohe statische und dynamische Belastungen machen ihnen dabei das Leben schwer. Mit exzellenten, auf den jeweiligen Anwendungsfall angepassten Eigenschaften wie maßgeschneiderte Streckgrenze, Zugfestigkeit und Zähigkeit halten die Hochleistungsbleche von Dillinger solchen Dauerbelastungen nachhaltig stand. So begründen Bleche für anspruchsvollste Spezifikationen den Ruf von Dillinger als Qualitäts- und Technologieführer. Um auch künftige Anforderungen weiterhin auf diesem Niveau zu erfüllen, arbeitet das Traditionsunternehmen laufend an der Entwicklung neuer Produkte und innovativer Verfahren entlang der gesamten Wertschöpfungskette. Neben State-of-the-Art-Produktionsanlagen und Verarbeitungskompetenz stehen dafür die umfangreichen F&E-Aktivitäten des Hightech-Stahlherstellers — intern oder in Zusammenarbeit mit Forschungsinstituten und Universitäten. Durch Entwicklung innovativer Verfahren und Anwendung neuer Erkenntnisse werden regelmäßig die Grenzen des Machbaren erweitert.
Stahleigenschaften per Design
Einen Schwerpunkt auf der Suche nach neuen, immer noch besseren Lösungen bildet seit 2015 die Forschungskooperation des Unternehmens mit der Universität des Saarlandes (UdS) und dem Material Engineering Center Saarland (MECS). Damals rief Dillinger eine dreijährige strategische Partnerschaft mit drei Instituten für Materialwissenschaft und Werkstofftechnik ins Leben und förderte diese mit knapp einer Million Euro. Jetzt schrieb das Unternehmen diese erfolgreiche Kooperation durch eine Anschlussförderung in gleicher Höhe für weitere drei Jahre fort. Ziel dieses integrierten Forschungsprojektes ist die systematische Erweiterung des mikrostrukturbasierten Werkstoffdesigns durch gezielte Gefüge- und Eigenschaftsmodellierung von Spezialstählen. Die innere Beschaffenheit dieser Stähle ist der Schlüssel zur Entwicklung innovativer Eigenschaftsprofile. Über das objektive Verständnis der Mikrostruktur und der sie beeinflussenden Parameter kann diese über den entsprechend modifizierten Herstellungsprozess präzise auf kundenspezifische Rahmenbedingungen eingestellt werden. Um diese Einsicht in die inneren Strukturen kontinuierlich weiter auszubauen, arbeiten die drei beteiligten Lehrstühle der Universität des Saarlandes an der Entwicklung innovativer Analysetechniken, Simulationsverfahren und Materialmodelle. Diese verzahnen sie nicht nur miteinander, sondern auch mit den anwendungsorientierten Forschungsaktivitäten von Dillinger. Per Simulation verknüpfen sie Prozessphasen und Produkt, um so die Mikrostruktur und damit die gewünschten Produkteigenschaften zu modellieren. Die Simulation kann bei der Blechherstellung deutlich schneller als mit realen Versuchen und vor allem exakt reproduzierbar entsprechend realisiert werden. Die Erkenntnisse, über Jahre aufgebautes Wissen sowie per Modellierung und Simulation gewonnene neue Einsichten ermöglichen bislang nicht denkbare Entwicklungssprünge. Mit ihnen kann Dillinger steigende Kundenanforderungen künftig präziser, flexibler und innovativer als je zuvor beantworten. Der Werkstoffcharakterisierung und -klassifizierung widmet sich der Lehrstuhl für Funktionswerkstoffe unter der Leitung von Professor Frank Mücklich, der auch die Koordination der Forschungsprojekte übernommen hat. Die Werkstoffbehandlung steht im Mittelpunkt der Forschungen am Lehrstuhl für experimentelle Methodik der Werkstoffwissenschaften, den Professor Christian Motz leitet. Die mechanische Werkstoffmodellierung ist der Forschungsschwerpunkt am Lehrstuhl für Technische Mechanik unter Federführung von Professor Stefan Diebels.
Gefüge-Klassifizierung auf Nanoebene
Basis für die Verknüpfung von Herstellungsprozess, innerer Beschaffenheit und Produkteigenschaften des Stahls ist die objektive Beschreibung der Mikrostruktur nach Zusammensetzung, Anzahl, Art und Verteilung ihrer Bausteine. Dazu arbeitet das Forscherteam um Professor Mücklich an der Entschlüsselung der de facto grenzenlosen geometrischen Vielfalt des Gefüges auf Mikro- und Nanoebene. Um diesen Parametern auf den Grund zu gehen, untersuchen die Wissenschaftler die Gefügestruktur bis ins kleinste Detail. Durch reproduzierbare Kontrastierung machen sie das Gefüge sichtbar und ermöglichen so eine sichere Quantifizierung der Gefügebausteine. Diese bergen die Geschichte des Herstellungsprozesses vom Nanometer- bis Mikrometer-Bereich. Die entwickelten Analysetechniken erlauben, den exakten Aufbau der Mikrostruktur darzustellen, also das Gefüge chemisch, kristallographisch und geometrisch abzubilden, auszulesen und objektiv zu bewerten.
Maschinelles Lernen
Im Rahmen des ersten Förderprojektes wurde zu diesem Zweck das Gefüge in den Oberklassen Ferrit, Perlit, Bainit und Martensit kontrastiert, segmentiert und mittels entsprechend entwickelter Data-Mining-Methoden klassifiziert. Die dafür genutzten Daten basierten auf den individuellen Pixel-„Umgebungen“ oder auch speziellen geometrischen Besonderheiten (Morphologievarianten) der untersuchten Gefügebausteine. Mit der zu ihrer systematischen und objektiven Beurteilung ebenfalls entwickelten Auswertemethode unter Nutzung von modernen Werkzeugen des maschinellen Lernens können nun 60 Prozent der Dillinger Stähle automatisiert analysiert und objektiv klassifiziert werden. Im jetzt angestoßenen Folgeprojekt optimieren und erweitern die Forscher dieses Lehrstuhls das zuvor erarbeitete Data-Mining-Konzept, indem sie sich der Untersuchung und Klassifizierung der bainitischen Substrukturen nach Gefügeart, Größe und Zusammensetzung widmen. Dazu werden diese Substrukturen in weitere Unterklassen unterteilt, um feinste Gefügeunterschiede korrekt zu erfassen und zu klassifizieren. Mit dem Ergebnis werden weitere 15 Prozent der Stahlgefüge automatisiert klassifizierbar sein.
Über mathematische Modelle zum Idealgefüge
Die Forscher um Professor Motz untersuchen den Einfluss von Parametern wie chemische Zusammensetzung, Wärmebehandlung, Prozesszeiten und Walztemperaturen auf die Mikrostruktur und damit letztendlich auf die mechanischen Eigenschaften durch Methoden der physikalischen Prozesssimulation. Mit mathematischen Modellen beschreiben sie, wie sich das Gefüge der Spezialstähle während des Produktionsprozesses bei den einzelnen Behandlungsschritten verändert. Basierend auf den Untersuchungen, wie Temperaturunterschiede bei der Verformung oder unterschiedliche Walztechniken Eigenschaften wie Festigkeit beeinflussen, wird die Veränderung der Austenitkorngröße und damit die Gefügeentwicklung modelliert. Im Rahmen des zweiten Förderprojektes wird die Gefügeentwicklung um die Vorgänge beim Fertigwalzen erweitert.
Für ausgewählte Legierungskonzepte und Prozessrouten ermöglicht die physikalische Prozesssimulation die Vorhersage und Kontrolle des Austenitzustands während der Prozessschritte. Dafür wird die Simulation um die Betrachtung der Größe einzelner Austenitkörner, ihrer Streckung und ihres Verformungszustandes erweitert und damit die Bandbreite der modellierbaren Stähle erheblich erweitert. Die Erkenntnisse werden durch Dillinger in das Walzmodell implementiert, um die Entwicklung der Mikrostruktur im Herstellungsprozess zu steuern. Das so gewonnene Verständnis der Prozessparameter und Einflussfaktoren ist der Schlüssel, um künftig die Prozessparameter optimal auf das vom Kunden gewünschte Eigenschaftsprofil des Stahls einzustellen.
Simulation von Mikroeffekten
Die Forscher am Lehrstuhl von Professor Diebels widmen sich der Untersuchung der Korrelation von Gefüge und Eigenschaften bei Dualphasenstählen. Dadurch wird das mechanische Verhalten neuer Stahlsorten schon während ihrer Entwicklung vorhersagbar. Im ersten Förderprojekt wurde eine Methode entwickelt, um die Fließkurve, also die Entwicklung der Verformung bei Belastung der Dillinger Stähle, mit einem mathematisch-physikalischen Modell beschreiben zu können. Dieses phasenbezogene, dreidimensionale Modell auf Basis der Gefügeparameter Phasenanteil, -größe, -morphologie und -verteilung bestimmt das makroskopische, mechanische Verhalten. Das Folgeprojekt erweitert die Simulation von Mikroeffekten um Effekte von Kornstruktur-dominierten Stählen. Dazu ist es notwendig, das bisherige phasenbasierte Modell feiner aufzulösen und kleinere Bereiche sowie deren individuelle Eigenschaften zu berücksichtigen. Voraussetzung hierfür ist die Abbildung der kristallografischen Kornstruktur des Ferrits. Um seine Eigenschaften in Abhängigkeit der Mikrostruktur möglichst exakt vorauszusagen, werden unterschiedliche numerische Verfahren ausgetestet. So wird es möglich, die Verformungen innerhalb eines Korns ebenso wie die Wechselwirkungen mit den Nachbarkörnern zu simulieren. Der permanente Abgleich von Simulation und Experimenten gewährleistet die Zuverlässigkeit dieser Eigenschaftsprognose. Das erlaubt künftig auch, die Fließkurve bei komplexeren Mikrostrukturen vorherzusagen.
Forschungskooperation 4.0
Die Zusammenarbeit zwischen Dillinger und den Forschungsteams der Universität des Saarlandes erweist sich gleich in mehrfacher Hinsicht als für alle Beteiligten gewinnbringend: Die systematische Erweiterung des mikrostrukturbasierten Werkstoffdesigns erschließt Dillinger ein intelligentes Werkzeug für die Entwicklung und Herstellung neuer, anspruchsvoller Spezialstähle. Es ergänzt optimal das datenbasierte Stahldesign, welches auf Erfahrungen und Referenzen beruht. Das mikrostrukturbasierte Design ermöglicht dabei die Gestaltung und Realisierung völlig neuer Eigenschaftsprofile. Das Verständnis der Mikrostruktur und mikrostruktureller Mechanismen auf Basis neuer, gesicherter Analysemethoden gestattet dem Stahlhersteller, durch Modellierung und Simulation konkrete Eigenschaftsprofile auf ihre Eignung für den Anwendungsfall zu prüfen und alle Produktionsschritte entsprechend zu gestalten. So kann Dillinger künftig genau definieren, wie das Gefüge eines Spezialstahls aussehen muss, um beispielsweise für arktische Einsatzbedingungen weiterhin bestens gewappnet zu sein.
Die enge Zusammenarbeit von Wissenschaft und Praxis überführt die theoretischen Überlegungen unmittelbar in die Anwendung und umgekehrt fließen Praxisergebnisse direkt wieder in die Arbeit der Forscher mit ein. Nicht zuletzt geht mit dem wissenschaftlichen Austausch auch ein Transfer der Köpfe einher. Zahlreiche Absolventen und Doktoranden der Universität des Saarlands arbeiten heute bei Dillinger und treiben so die permanente Innovation bei dem Hightech-Stahlunternehmen auch weiter voran.
Dillinger Hüttenwerke
Seit mehr als 330 Jahren lebt Dillinger eine einzigartige Leidenschaft für Stahl — vom Erz bis zum maßgeschneiderten Grobblech und einbaufertigen Element. Der laut Eigendefinition weltweite Qualitäts- und Technologieführer, dessen Stahlgüten mehrheitlich jünger als zehn Jahre sind, produziert mit 7.500 Mitarbeitern jährlich rund 2,3 Mio. Tonnen Rohstahl und 1,9 Mio. Tonnen Grobblech. Die extrem belastbaren Hochleistungswerkstoffe finden bevorzugt Einsatz im Stahlbau, Maschinenbau, Offshore, Offshore-Windkraft, Linepipe, Baumaschinen, Bergbau oder Kesselbau.