Massen in Bewegung
Ein Zementwerk bewegt pro Stunde rund 1.200 Tonnen Material. Gestein wird gemahlen, geschmolzen, gelagert, vermischt und schlussendlich als Zement verkauft.
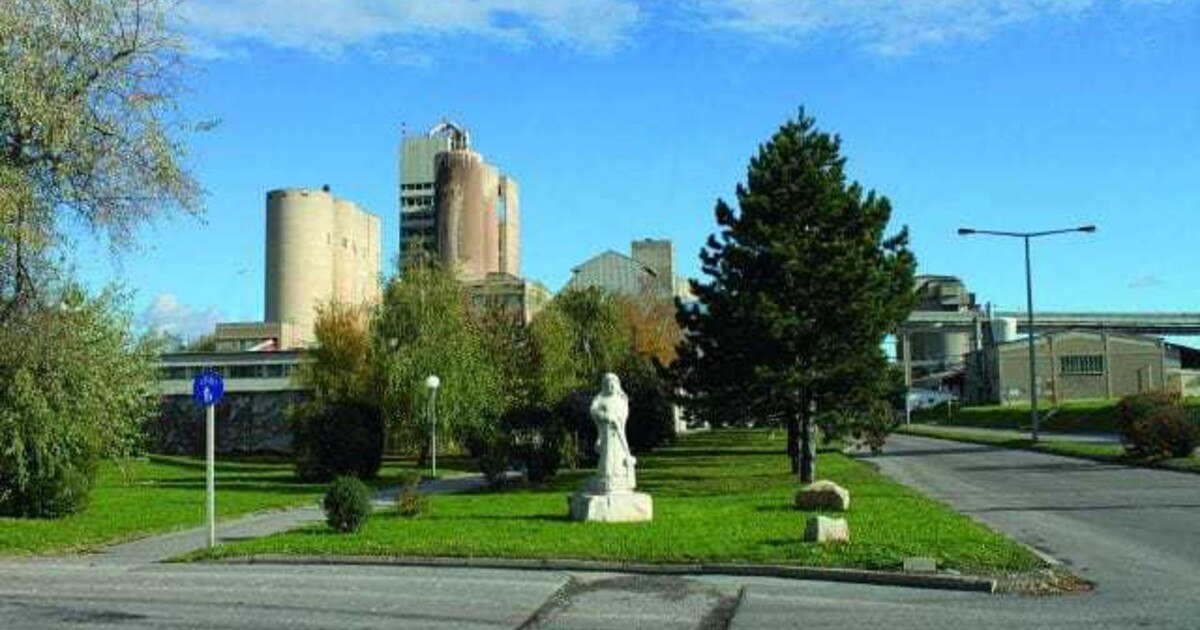
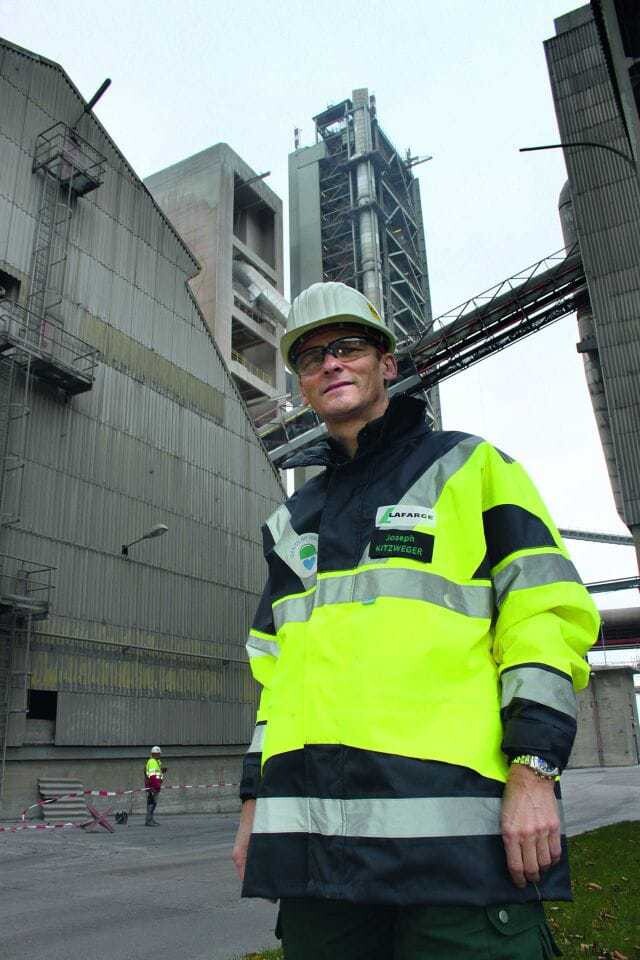
Von außen betrachtet, liegt das La-Farge-Zementwerk in Mannersdorf friedlich an den niederösterreichischen Ausläufern des Leithagebirges. Doch betritt man das Werk, spürt man sofort, dass alles stetig in Bewegung ist.
Alles außer Stillstand
Pro Stunde werden rund 1.200 Tonnen Materialien durch das Werk bewegt, eingeschmolzen oder gemahlen. Zeitgleich dreht sich ein Drehrohrofen elf Monate im Jahr, sieben Tage die Woche, 24 Stunden am Tag und verarbeitet bei 1.500 Grad Celsius Gestein in Zementklinker. „Für ein Zementwerk ist es das schlimmste, wenn Stillstand herrscht“, erklärt der Werksleiter Joseph Kitzweger. „Wir haben nach jedem Arbeitsschritt ein Lager, das etwaige Ausfälle abfangen kann.“
Deswegen hat das Werk unter anderem ein 120.000 Tonnen umfassendes Klinker- und ein 60.000 Tonnen schweres Zementlager. Diese sind auch notwendig, um eine Produktionskapazität von 1,3 Millionen Tonnen pro Jahr garantieren zu können. Damit kommt fast ein Viertel der gesamten österreichischen Zementprodukte von 5,5 Millionen Tonnen pro Jahr aus dem Werk in Mannersdorf. Doch gerade bei so großen Produktionsmengen gilt es, mit Rohstoffen sparsam umzugehen und anfallende Abgase geschickt zu filtern.
Alternative Wege
Zement besteht zu 80 Prozent aus Kalk und zu 20 Prozent aus Ton. Beide Materialien werden prinzipiell in den zwei hauseigenen Steinbrüchen abgebaut. Jedoch geht man gerade beim Ton neue Wege. Dieser wird zu einem Teil aus dem Ziegelsplitt alter Wiener Häuser gewonnen.
Auch beim Drehrohrofen, der der Klinkerproduktion dient, versucht man nachhaltig zu arbeiten. Normalerweise würde ein Ofen dieser Größe eine Lkw-Ladung Kohle in zwei Stunden verheizt haben. Um den Verbrauch an mineralischen Rohstoffen zu senken, werden mittlerweile zwei Drittel des Brennstoffbedarfs aus Ersatzbrennstoffen gewonnen. Verheizt werden vor allem Plastik, Tiermehl und Sonnenblumenschalen. Die anfallenden Abgase wiederum werden mithilfe von „Luftikus“, einer „selective catalytic reduction“-(SCR)-Anlage, von Stickoxiden (NOx) gereinigt. Dadurch wird ein NOX-Grenzwert von 0,2 Gramm pro Kubikmeter Abgas erreicht.
„Wir sind sehr stolz auf den Weg, den wir mit unserem Werk gehen, und sehen uns auch ein bisschen in einer Vorreiterrolle“, stellt Kitzweger fest. Ein Weg, der laut dem Werksleiter auch von allen Angestellten mitgetragen und immer wieder öffentlich Anrainern präsentiert und mit diesen diskutiert wird. „Es ist uns sehr wichtig, in direktem Kontakt mit der Gemeinde und den Menschen zu stehen, um möglichen Problemen vorzubeugen und bestehende zu bereinigen.“
Noch mindestens 50 Jahre
Insgesamt sind in dem niederösterreichischen Zementwerk rund 105 Mitarbeiter, zehn bis 15 Lehrlinge und 35 externe Mitarbeiter dauerhaft beschäftigt. Stehen die jährlichen Wartungen oder große Reparaturen, zum Beispiel am Drehrohrofen, an, steigt die Zahl der Mitarbeiter in kurzer Zeit stark an, da bis zu 200 externe vor Ort arbeiten. Dies wird auch mindestens für die nächsten 50 Jahre so bleiben, denn so lange halten die Ressourcen in den beiden Steinbrüchen des Zementwerks noch.