Trocknung im Rechner
Mithilfe eines „digitalen Zwillings“ optimiert Fundermax die Produktion seiner Compactplatten.
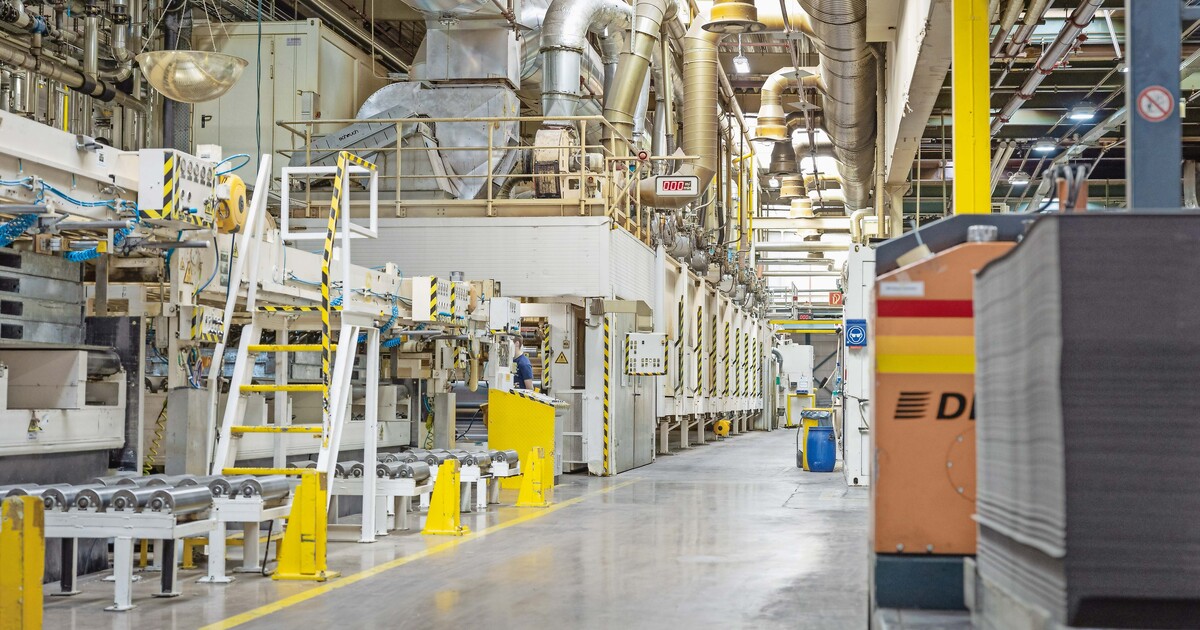
Bei der Herstellung von Schichtstoffplatten, auch als Kompaktplatten bekannt, wird in einem ersten Schritt Kraftpapier von der Rolle abgerollt, mit Phenolharz imprägniert, getrocknet und in Bahnen geschnitten. Diese Bahnen werden anschließend verschlichtet und unter hohem Druck und hoher Temperatur zur Platte verpresst, um gewünschte Dekorlagen ergänzt, zugeschnitten und ausgeliefert. Soweit der – sehr stark vereinfachte – Prozessablauf einer Kompaktplattenfertigung. Ein Vorgang, den Hersteller natürlich beherrschen, der aber dennoch Optimierungspotenziale in sich birgt.
Reale Bedingungen im Rechner nachstellen
„Das Imprägnieren ist ein physikalisch, aber auch chemisch recht komplexer Prozess“, sagt Harald Macheiner, Director Technical Department bei Fundermax. „Das Vernetzen des Harzes passiert einmal beim Trocknen der Papierbahnen und einmal beim Aushärten in der Presse. Das heißt, es ist sehr wichtig, den richtigen Vernetzungsgrad des Harzes zu bestimmen. Das basiert heute sehr stark auf Erfahrung.“ Um Erfahrung durch wissenschaftliche Strenge abzusichern oder zu ergänzen, hat Fundermax gemeinsam mit dem Research Center for Non-Destructive Testing und dem Austrian Institute of Technology ein Forschungsprojekt gestartet. Ziel war es, den Imprägnierprozess im Rechner als so genannten „digitalen Zwilling“ nachzustellen.
Anhand eines solchen virtuellen Gegenstücks lassen sich dann diverse Versuche durchführen. Beispielsweise kann man per Knopfdruck Umgebungsparameter wie Temperatur, Luftmenge oder Luftfeuchtigkeit verändern und sehen, wie sich diese auf das Ergebnis auswirken. „Mithilfe des digitalen Zwillings können reale Versuchs- und Umgebungsbedingungen nachstellen und somit belastbare Aussagen treffen“, erklärt Macheiner. „Er erlaubt uns, sehr genaue Vorhersagen zu treffen, welche Auswirkung die Änderung eines Parameters haben wird. Ich sehe im digitalen Zwilling, welche Auswirkungen es auf die Platte hat, wenn sich die Umgebungstemperatur zum Beispiel um zehn Grad ändert. Ob es dann zu Krümmungen oder Oberflächenveränderungen kommt, die sogar dazu führen können, dass die Platte Ausschuss ist.“ Das ginge am realen Objekt zwar grundsätzlich auch, wäre allerdings aufwändiger und würde Ausschuss erzeugen. Zudem lassen sich nicht alle realen Umgebungsparameter so exakt kontrollieren, wie es für einen methodisch sauberen Versuch nötig wäre.
Weniger Energieverbrauch
Ziele des Projektes ist es, die Parameter des Imprägnierprozesses so weit zu optimieren, dass bei gleicher Qualität weniger Energie eingesetzt werden muss. „Man kann auf drei Weisen trocknen“, sagt Macheiner. „Durch Temperatur, durch Luftmenge oder durch Reduktion der Auftragsmenge. Dieses Dreigestirn muss in einem optimalen Punkt zusammengeführt werden, damit am Ende in der Presse das richtige Produkt entsteht.“ Seit rund sieben Jahren beschäftigt sich Fundermax mit der Technologie des digitalen Zwillings. Die Resultate aus dem laufenden Projekt sind bereits in den realen Imprägnierprozess eingeflossen und haben zu Energieeinsparungen zwischen 20 und 30 Prozent geführt. Das nächste Vorhaben ist die digitale Modellierung des Pressens. Damit eines Tages die komplette Prozesskette als digitaler Zwilling vorhanden ist und genutzt werden kann.