Der neue Kollege
Was Cobots wirklich können, für wen sich die Anschaffung lohnt und warum ihnen die Pandemie zum endgültigen Durchbruch verhelfen könnte, haben wir zusammengefasst.
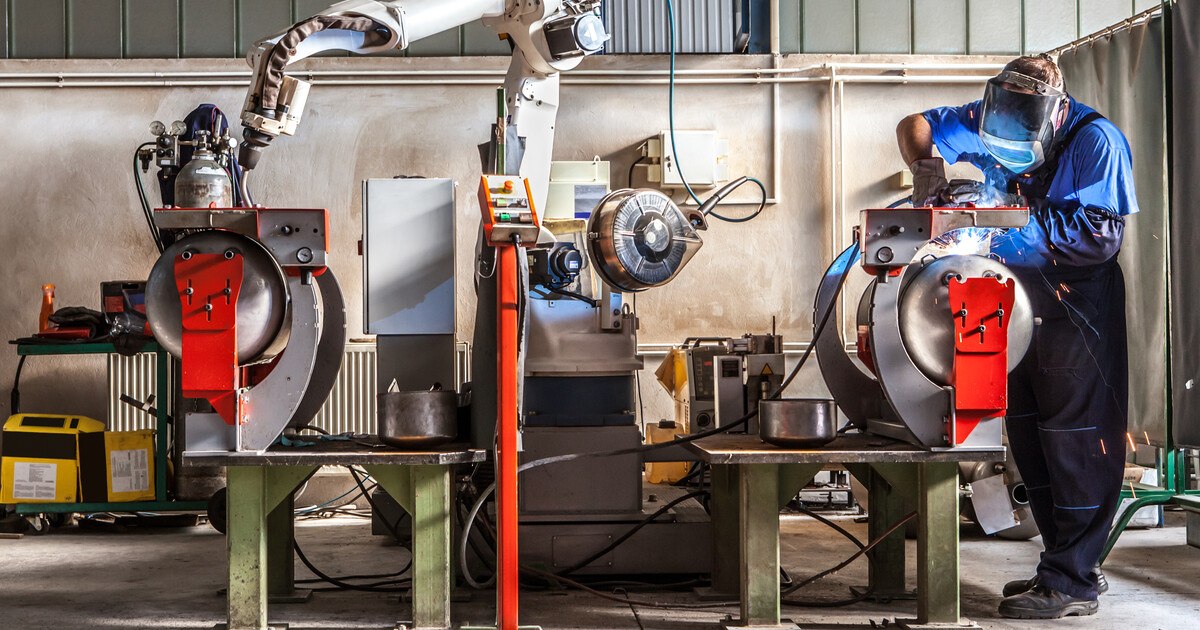
Die Herausforderungen an Produktionsunternehmen sind in und nach der Coronakrise grundlegend dieselben wie vor der Pandemie. Trotzdem – der Handlungsdruck durch zunehmenden Wettbewerb, gestiegene politische Volatilität und nicht zuletzt den Fachkräftemangel hat sich durch die Pandemie verschärft. Kollaborative Technologien, die flexible Einsatzmöglichkeiten versprechen, können Unternehmen helfen, in unruhigen Zeiten den Kurs zu halten und die nötige Stabilität zu wahren. Die sogenannten Cobots – derzeit vor allem in der Industrie in aller Munde – lassen sich einfach bedienen, sind vielseitig einsetzbar und amortisieren sich schnell. Dadurch machen sie sich auch für KMU bezahlt.
Als Cobots – kurz für „collaborative robots” – bezeichnet man Roboter, die direkt, im Idealfall ohne Schutzzaun, mit menschlichen Kollegen zusammenarbeiten. Sie lassen sich schnell umrüsten und erledigen mit Peripheriegeräten wie Greifern oder Kamerasystemen unterschiedliche Aufgaben – sei es in der Montage, der Qualitätsprüfung oder der Maschinenbeschickung. Aufgrund ihrer Leichtbauweise lassen sich die Roboterarme einfach bewegen und an verschiedenen Orten in der Fertigung einsetzen. So können Unternehmen Prozesse flexibler gestalten und ihre Produktion bei Bedarf schnell an die Gegebenheiten anpassen. „In der kollaborativen Fertigung, also wenn sich Mensch und Maschine den Arbeitsraum teilen und beispielsweise gemeinsam an einem Werkstück arbeiten, kann ein Cobot auf unterschiedliche Weise entlasten. Das Ziel deren Einsatzes ist aber häufig qualitativ, betreffen also etwa die Ergonomie oder geben Unterstützung bei ermüdenden Tätigkeiten“, erklärt Felix Strohmeier, Leiter der Forschungsgruppe „Internet of Things“ bei Salzburg Research und für den Bereich „Kollaborative Fertigung“ im Digitalen Transferzentrum Salzburg (DTZ).
Industrieroboter hinter Schutzzäunen bleiben uns sicher weiterhin erhalten, denn durch die Trennung von Menschen können sie sehr schnell und effizient arbeiten.
Die häufigste Cobot-Anwendung ist nach wie vor das Be- und Entladen von Maschinen und auch in der Montage können sie eine wichtige Rolle spielen. Hier unterstützen sie oft beim Kommissionieren der richtigen Teile, was wiederum das Potenzial hat, die Qualität direkt zu erhöhen. Denn ein Roboter greift nicht in die falsche Kiste und reicht dadurch ein falsches Teil. Ebenfalls eingesetzt werden Cobots etwa bei Verpackungsarbeiten, bei der Palettierung und Sortierung. Ein weiterer Bereich ist auch das Schweißen. Hier kann der Cobot seine volle Stärke ausspielen, da er genauere Ergebnisse erzielt als das manuelle Schweißen und dieses zudem nicht von der Tagesform des Schweißers abhängt.
Trotz vielfältiger Einsatzmöglichkeiten, als Ersatz traditioneller Industrieroboter sind Cobots nicht geeignet. „Industrieroboter hinter Schutzzäunen bleiben uns sicher weiterhin erhalten, denn durch die Trennung von Menschen können sie sehr schnell und effizient arbeiten“, erklärt Strohmeier. Cobots dagegen können durch das Wegfallen der Barrieren neue Anwendungsgebiete erschließen.“ Der Nutzen dabei sei ganz klar die nahtlose Integration von robotischen Prozessen in die Umgebung von Menschen und Tieren mit dem daraus resultierenden geringeren Platzbedarf und dem Wegfallen von Übergabepunkten. Nicht zuletzt deshalb könnten auch KMU davon profitieren. „Gerade in KMU können Leichtbauroboter ein günstiges „Allround-Werkzeug“ sein, wenn sich Tasks öfters ändern.“ Grundsätzlich gelte dafür: Je öfter ein konkreter Task wiederholt werden soll, desto eher eignet sich dafür der Einsatz von Robotern. „Es gibt Beispiele von Cobots in Backstuben, für das Be- und Entladen von Maschinen oder auch für Schleifarbeiten, bei denen der genaue Anpressdruck wichtiger ist als eine präzise Bahnführung. Diese Fähigkeit haben die meisten Cobots durch ihre Kraftbegrenzungen schon eingebaut.“
Trotz ihrer Vorteile, den Durchbruch am Markt haben Cobots bis jetzt noch nicht geschafft. Für Titanilla Komenda, Robotik-Ingenieurin am Fraunhofer Institut, hängt das vor allem mit zwei Dingen zusammen. „Man muss schon sagen, dass es derzeit noch einiges an Engineering-Aufwand braucht, damit Cobots ihr volles Potenzial ausschöpfen können. Gleichzeitig sind aber auch die Sicherheitsrichtlinien bzw. Normen noch nicht so weit, um Cobots vor allem einen flexiblen Einsatz zu ermöglichen.“ So seien die Maschinen etwa noch nicht so intelligent, dass sie neue Teile selbst erkennen würden oder sich selbstständig an eine Umgebung anpassen könnten. „Derzeit braucht es noch einen Mensch, der diese Dinge einprogrammiert.“
Zudem geht es in Zukunft auch darum, Cobots mobil zu machen, um etwa größere Reichweiten zu erzielen. „Die aktuellen Normen erlauben das Bewegen und Arbeiten eines mobilen Roboterarms nur dann, wenn der mobile Unterbau stillsteht oder überhaupt fix verankert ist“, erklärt Felix Strohmeier. Für dieses Problem sei es wichtig, die jeweiligen Bewegungsmodelle genau zu beherrschen und die damit zusammenhängenden Gefahren genau einschätzen und ausschließen zu können. Das geschehe mit verbesserter Sensorik, wie sie zum Beispiel auch im autonomen Fahren eingesetzt werde. „Um diese Flut an Sensordaten auch beherrschen zu können, werden derzeit Methoden des maschinellen Lernens eingesetzt, um neue Situationen auf Basis von erlerntem Verhalten richtig einschätzen zu können.“
Auch die Sicherheit spielt für die Markteinführung eine zentrale Rolle. Grundsätzlich ist die Mensch-Roboter-Kollaboration dabei nach der technischen Spezifikation ISO TS 15066 geregelt. Nach dieser geltenden Norm müssen die Cobots vier grundsätzliche Betriebsmodi ausführen, die auch miteinander kombiniert werden können. Sobald ein Mensch also in den Arbeitsraum des Roboters eindringt, muss ein sicherer Stopp ausgeführt werden. Der Cobot kann dann beispielsweise mit der Hand geführt werden, um Zielpositionen zu definieren. Kräfte und Leistung müssen bei Kontakt aber soweit reduziert werden, dass für den Menschen keine Gefahr besteht. Die Gefahr wiederum wird je nach Geschwindigkeit und Abstand zum Menschen entsprechend beurteilt. Dabei muss nicht nur der Roboter selbst, sondern auch das transportierte Werkstück oder ein möglicherweise gefährliches Werkzeug am Greifarm des Roboters berücksichtigt werden. Schweißroboter oder auch spitze, scharfkantige Werkzeuge sind tendenziell gefährlich für kollaborative Tätigkeiten. „Die große Herausforderung ist es daher, nutzbringende Helfer, die über entsprechende Stärke und Schnelligkeit verfügen, sicher zu machen. Viele Cobots sind von vornherein in Leichtbauweise ausgeführt, um die Gefahren zu reduzieren. Zusätzlich helfen audiovisuelle Signale um auf Gefahren aufmerksam zu machen“, sagt Strohmeier.
Derzeit in der Interaktion am meisten fortgeschritten sind laut Strohmeier mobile Service-Roboter. Sie können meistens nur geringe Traglasten bewältigen, der Fokus liegt bei diesen Modellen in der sozialen Interaktion. Forscherteams arbeiten weltweit daran, eine möglichst „natürliche“ Zusammenarbeit bzw. Interaktion zwischen Mensch und Roboter zu erreichen. „Oft eignen sich dazu dieselben Modelle, die zwischenmenschlich oder auch im Zusammentreffen mit Tieren beobachtet werden können. Prinzipiell gilt: Je größer und gefährlicher das Gegenüber wirkt, desto größer ist die anfängliche Scheu, die jedoch durch längere Zusammenarbeit und Schulungen abgebaut werden kann. Der Mensch entwickelt im Laufe der Zusammenarbeit ein Gefühl dafür, welche Gefährdung von unterschiedlichen Robotern ausgeht.“
Natürlich wird eine Krise wir die Corona-Pandemie, die technischen Herausforderungen nicht lösen. Aber man beginnt langsam das Potenzial der Mensch-Roboter-Kollaboration zu erkennen.
Wann diese Herausforderungen überwunden sind, steht derzeit noch in den Sternen. Eine neue Chance hat sich aber mit der Pandemie aufgetan. Das zeigen aktuell auch Beispiele aus der Praxis, wie etwa der Automobilhersteller SEAT: Das Unternehmen stellte im März dieses Jahres eine seiner Montagelinien kurzfristig um und produzierte statt Autoteilen 300 Beatmungsgeräte pro Tag. Am Ende der Linie hat der Automobilriese einen Cobot, den UR10e, installiert, um eine Qualitätsprüfung des Verriegelungsmechanismus am Schaltkasten der Einheit durchzuführen. Ein ähnliches Beispiel liefert die niedersächsische MSK Industrie Service & Consulting, die normalerweise Komponenten für die Automobilindustrie herstellt. Als die Pandemie begann und der Bedarf an Atemschutzmasken sprunghaft stieg, beteiligte sich das Unternehmen an einer Ausschreibung des Bundesgesundheitsministeriums. MSK bekam den Zuschlag und produziert heute dringend benötigte FFP2-Masken. Ein sogenannter UR5e unterstützt bei deren fachgerechter Verpackung: Der Roboterarm nimmt die fertigen Masken aus der herstellenden Maschine und legt sie in einem genau definierten Winkel in die Verpackungsmaschine ein. „Die Praxis zeigt, dass die Pandemie durchaus ein Anstoß für Unternehmen sein kann, um umzudenken“, sagt Titanilla Komenda. „Natürlich wird eine Krise wir die Corona-Pandemie, die technischen Herausforderungen nicht lösen. Aber man beginnt langsam das Potenzial der Mensch-Roboter-Kollaboration zu erkennen.“ Darüber hinaus würden es die Roboterarme erlauben, Abstandsregeln in der Fertigungshalle einzuhalten und variablere Produktionszeiten zu fahren, wenn Schichten aufgeteilt werden, damit nicht zu viele Menschen gleichzeitig in der Fertigung arbeiten.
Und auch jenseits der Industrie sorgen sie für sichere Prozesse: In Portland zum Beispiel bereitet ein UR-Cobot namens Jarvis Kaffee-Spezialitäten zu. Café-Betreiber Joe Yang bemerkte, dass nach dem Ausbruch von COVID-19 immer weniger Menschen in seinen Coffeeshop kamen. Daraufhin beschloss er, seine Kunden zu schützen, indem er einen Cobot als Barista engagierte. So reduziert er die sozialen Kontakte beim Kaffee-Kauf und senkt das Infektionsrisiko für seine Kunden.