Kräftige Heavy-Duty-Spezialisten
Lösungen und Anwendungsbeispiele für komplexe Bauteile. METALL gibt einen Überblick.
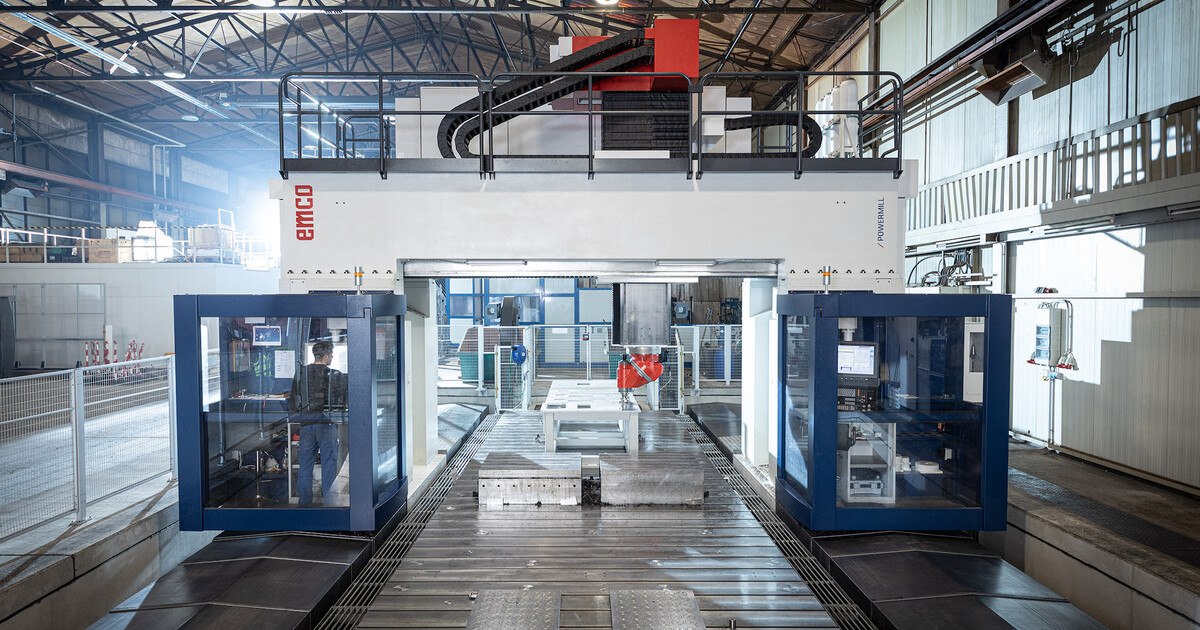
Große Bauteile aus Stahl, Titan oder schwer zerspanbaren Aluminiumlegierungen sowie komplizierte Geometrien lassen sich mit dem richtigen Zusammenspiel von Werkzeug und Maschine meistern. Der nachfolgende Überblick präsentiert Maschinen und Anwendungsbeispiele als Inspiration für derartige Heavy-Duty-Aufgaben oder auch Schwerzerspanung.
CHIRON: Solide Basis für Heavy-Duty
Vor einigen Jahren hat Chiron mit der Baureihe 16 den Grundstein für eine ganze Produktreihe für die Schwerzerspanung gelegt. Der Anspruch an die Bearbeitungs- und Fräs-Dreh-Zentren der Heavy-Klasse: stabil, präzise, prozesssicher und hochproduktiv.
Zur Orientierung ein Blick auf das Teilespektrum, das die deutschen Entwickler der Baureihen für das Schwerzerspanen im Blick hatten: Fahrwerkskomponenten und Strukturbauteile. Welche „Must-haves“ fordern Anwender, die solche Bauteile fertigen? Es sind drei Punkte:
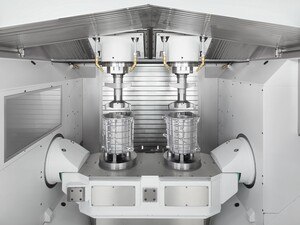
• Große Werkzeugmagazine: Es sind viele, oft große Werkzeuge im Spiel und die Bearbeitungszeiten sind lang.
• Prozesssicherheit, Präzision, Qualität: Hohe Zerspanvolumen und Werkstoffe verlangen Maschine und Werkzeug an Leistung und Stabilität alles ab.
• Flexibilität und Produktivität: ein praxistaugliches Konzept für automatisiertes Werkzeug- und Werkstückhandling für sowohl Varianten- als auch Serienfertigung.
„Über diese speziellen Herausforderungen haben wir mit vielen Anwendern gesprochen“, berichtet Gerhard Ulmer, Vertriebsbereichsleiter Branchen bei Chiron. „Im Ergebnis haben wir heute mit den Baureihen eine grundsolide, vielseitige Basis für die steigende Nachfrage an Heavy-Duty-Anforderungen im Produktprogramm. Und das Plus, das wir den Anwendern mit unseren Turnkey-Lösungen bieten können, ist die hohe Produktivität beim schweren Zerspanen.“ Ein Beispiel aus der Praxis zeigt, dass sich Stabilität auf allen Ebenen signifikant auf die Produktivität auswirkt. Eine DZ 16 W mit HSK-A63 beweist sich bei einem Anwender in der Fertigung von Pressbacken, sogenannten Crimp Jaws. Diese sind in hydraulischen Crimp-Werkzeugen für Arbeiten an potenziell spannungsführenden Leitungen verbaut. Der Prozess ist für eine automatisierte Variantenfertigung von zwölf verschiedenen Bauteilen aus 42CrMo4 ausgelegt. Es wird wie zuvor auch doppelspindlig zerspant und mit dem Wechseltisch hauptzeitparallel be- und entladen und umgespannt. Die thermische, statische und dynamische Stabilität, wie sie die Baureihe 16 bietet, verschiebt die Leistungsgrenze definitiv nach oben. Sei es in der Dynamik, die ein High-Feed-Fräser fordert, oder in der Steifigkeit und dem Drehmoment, den ein maximales Zeitspanvolumen Q spanender Igelfräser braucht. Unterm Strich stehen 15 Prozent mehr Teile in der gleichen Zeit. Das zahlt sich aus und stärkt den Kunden im Wettbewerb. Manuel Jans, Projektierungsleiter der Chiron Group im Kompetenzteam Schwerzerspanung: „Die Baureihen 16 und 22 sind seit ihrer Markteinführung erfolgreich am Schwerzerspanen. Unter anderem in der Bearbeitung von Stator- und Motorgehäusen für E-Fahrzeuge.“ Wo die Chiron Group mit ihrem Schwerzerspanungsprogramm hin will, zeigt auch die Weiterentwicklung. Seit Kurzem steht Komplettbearbeitern unter den Schwerzerspanern auch eine Mill-Turn-Version der Baureihe 22 zur Auswahl: Zur doppelspindligen Fräspower mit einem Zeitspanvolumen Q von 1.280 Kubikzentimetern pro Minute und Spindel kommt die volle Drehleistung mit 610 Newtonmetern und 1.800 Umdrehungen pro Minute. Für die Maschinen stehen seites Chiron auch Automationslösungen parat: individuelles Werkzeug- und Werkstückhandling mit Roboter, Plattenspeicher, Hintergrundmagazin sowie Greifer- und Vorrichtungswechselstationen.
EMCO: Mit der Powermill in die Zukunft
Südstahl, ein mittelständischer Spezialist für die Verarbeitung von Stahl und Anbieter von Lagersystemen hat in eine neue Werkzeugmaschine investiert. Die alte Bearbeitungs- und Fräsmaschine wurde ausgetauscht gegen die moderne und flexible Portalfräsmaschine Powermill von Emco. Im Vorfeld dieser Anschaffung galt es eine Vielzahl an Kriterien zu analysieren und das am Markt verfügbare Angebot zu sondieren. „Dabei ist die Auswahl des passenden Maschinentyps für uns als Auftragsfertiger eine große Herausforderung: wir müssen auch in den kommenden Jahren die Anforderungen der Kunden bewältigen, ohne genau zu wissen, in welche Richtung sich diese Anforderungen entwickeln. Somit spielt ein hohes Maß an Flexibilität eine entscheidende Rolle“, erläutert Ulrich Käuferle. „Die Wettbewerbsfähigkeit wird langfristig durch eine hohe Produktivität bei tragfähigen Kosten gesichert. Entscheiden wir uns für das falsche Konzept, greifen unsere Kunden auf andere Anbieter zurück“, so der Südstahl-Geschäftsführer weiter. Außerdem wolle man seinen Fachkräften einen modernen und zukunftsorientierten Arbeitsplatz bieten.
Nach einem aufwändigen Auswahlprozess unter Einbeziehung aller im Unternehmen verfügbarer Expertise fiel die Wahl letztendlich auf die Powermill HPC-3 des Herstellers Emco. Für dieses hochmoderne Produkt sprach zum einen die „Box-in-Box“-Konstruktion, die eine maximale Präzision bei der Bearbeitung gewährleistet. Zum zweiten überzeugt die „Powermill“ dadurch, dass sie sehr flexibel in verschiedensten Anwendungsbereichen zum Einsatz kommen kann: dies sowohl in der Luft- und Raumfahrttechnik als auch im allgemeinen Maschinenbau.Bei der Powermill handelt es sich um eine Universalfräsmaschine für die effiziente Bearbeitung von sperrigen und schweren Werkstücken. Hierbei bietet die massive Struktur dieser Portalfräsmaschine vielfältige Einsatzmöglichkeiten – bei gleichzeitiger Dynamik. Ihr kompaktes Design ermöglicht eine einfache Werkstückhandhabung, Einrichtung und Aufspannung. Die Powermill verfügt über zahlreiche Optionen und Systeme wie unter anderem einen Fräskopfwechsler, eine zweifache CNC-Plattform sowie einen Werkzeugwechsler mit 60 Plätzen. Der maximale Bearbeitungsbereich umfasst 10.000 x 3.000 x 1.500 Millimeter.
Die Powermill wurde bei Südstahl zusätzlich mit einer Vorrichtung für die Pendelbearbeitung ausgestattet. „Somit können wir die Rüstzeiten optimieren und die Laufzeiten der Anlage erhöhen“, erklärt Produktionsleiter Oliver Wetzenbacher. „Mit dieser Ersatzinvestition haben wir die Weichen in die Zukunft gestellt“, kommentiert der technische Leiter Peter Birkner die Neuanschaffung. „Mit der Präzision dieser Maschine erfüllen wir die geforderten Qualitätsansprüche unserer Kunden. Und gleichzeitig erweist sich die neue Fräsmaschine durch das optimierte Rüsten und Einrichten für unsere Mitarbeiterinnen und Mitarbeiter weitaus bedienerfreundlich“, so Peter Birkner abschließend.
GF Machining: Schwere Zerspanung bedeutet Hochleistungsfräsen
Hochleistungsfräsen steht für eine hohe Abtragrate beim Schruppen, hohe Präzision bei großen, schweren Teilen und engste Toleranzen nach der Feinbearbeitung. Ebenso steht der Begriff bei GF Machining Solutions für Oberflächengüte bei leichten oder schweren Teilen und eine flexible Teileproduktion sowie hohe Produktivität. Die Lösungen von GF Machining Solutions im Bereich Schwerzerspanung sind zum Beispiel die fünfachsigen Fräsmaschinen-Baureihen Mikron Mill S U und Mill X U sowie die dreiachsigen Baureihen Mikron Mill S oder Mill X. Diese arbeiten präzise mit hoher Dynamik. Die Maschinen sind leicht zugänglich und benötigen nur wenig Platz – ob als Einzelmaschine oder in Kombination mit einer Automatisierungszelle. Die serienmäßige AMC (Automated Machine Calibration, automatisierte Maschinenkalibrierung) sorgt für eine optimale Kalibrierung und die Kühlung aller Maschinenkomponenten hält den Prozess auch bei langen Fräs- und Schleifarbeiten stabil. Mit seinem Zerspanungs-Know-how und dem modernen Maschinenpark kann HLM sehr flexibel auf Kundenanforderungen reagieren und höchstmögliche Präzision und Qualität bieten. Mit GF als Partner hat man bereits seit den Achtzigerjahren die modernsten Maschinen im Einsatz und konnte seine Prozesse dank der neuen Technologien stets optimieren. Firmengründer Heinz Leuthold hat in eine Mikron Mill X 400 mit Schleiffunktion investiert, um im Bereich Koordinatenschleifen, kombiniert mit Hartfräsen wettbewerbsfähig zu bleiben. Auf der Maschine werden Elektroden bis zu gehärteten Werkstücken bearbeitet, vom Hartfräsen über Koordinatenschleifen bis zum Rundschleifen. Mit der Mill X 400 können die Rundschleifer entlastet werden, weil mit Mehrfachaufspannungen gearbeitet werden kann. Abgesehen davon müssen die Werkstücke nicht mehr von der Koordinatenschleifmaschine auf die Fräsmaschine verschoben werden, sondern können in einer Aufspannung bearbeitet werden. Der große Vorteil für HLM besteht darin, dass die Mill X 400 die bereits bestehenden Mikron Mill S 600 U und die Mill S 500 optimal ergänzt, weil sie die gleiche Spindel mit gleichen Werkzeugkonen und die gleichen Spannmittel besitzt und alle Maschinen mit derselben Heidenhain-Steuerung ausgerüstet sind. Somit ist alles standardisiert und es kann flexibel zwischen den drei Maschinen hin und her gewechselt werden. HLM kann dank der Option Ambient Robust Toleranzen von +/-0,002 Millimetern prozesssicher bearbeiten.
GROB: Trocken und nass
Der Doppelspindler G720F zählt zu den größten Maschinen bei Grob, prädestiniert für die parallele Bearbeitung von Rahmenstruktur- und Fahrwerksteilen, Batteriegehäusen sowie weiteren Bauteilen aus der Automobilindustrie (zum Beispiel Längsträger oder Castingteile aus Aluminiumlegierungen). Da kann die Motorspindel schon mal mit 18.000 Umdrehen pro Minute loslegen.
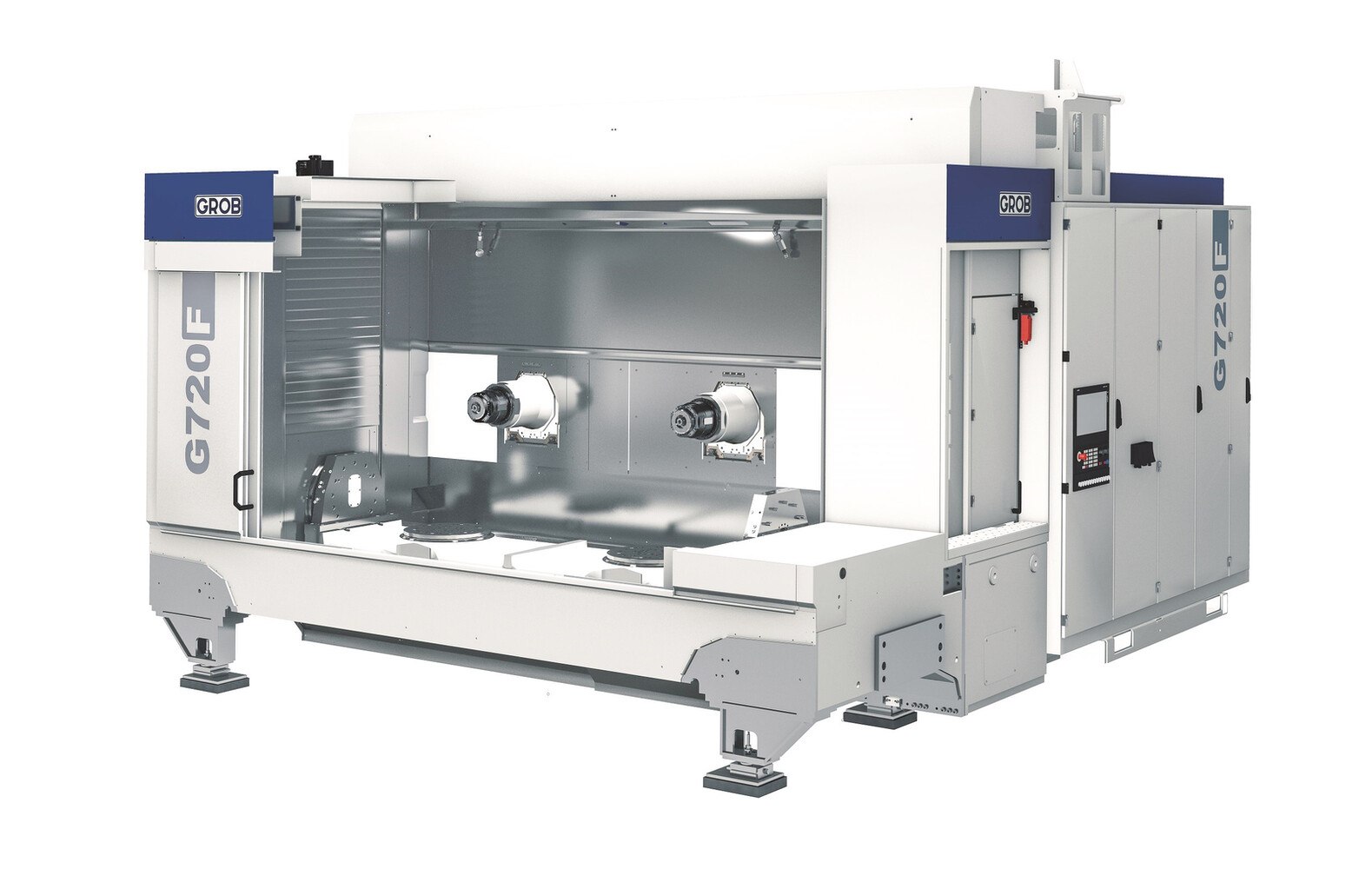
© GROB
Die A/B-Achskombination im Tisch garantiert einen freien Spänefall und eine optimale, was besonders für die Minimalmengen-Schmierung-Bearbeitung (MMS) geeignet ist. Grob verspricht mit dem hochbelastbaren Bearbeitungszentrum kurze Span-zu-Span-Zeiten. Ein großzügig ausgelegter Arbeitsraum nimmt auch die „schwren“ Brocken unter den Wrkstücken auf. Durch ihren optimalen Späneabtransport und die hohe Maschinendynamik eignet sich das platzsparednde 5-Achs-Bearbeitungszentren für die Trocken-, MMS- und Nassbearbeitung von Werkstücken. Ob alleinstehend oder im Verbund mit anderen Werkzeugmaschinen.
HEDELIUS: Werkstücke bis 4.000 Kilogramm
Mit einem beachtlichen Y-Verfahrweg von 1.100 mm besticht die Tiltenta 11 mit einem sehr großen Arbeitsraum, in dem auch massive Bauteile 4/5-achsig bearbeitet werden können.
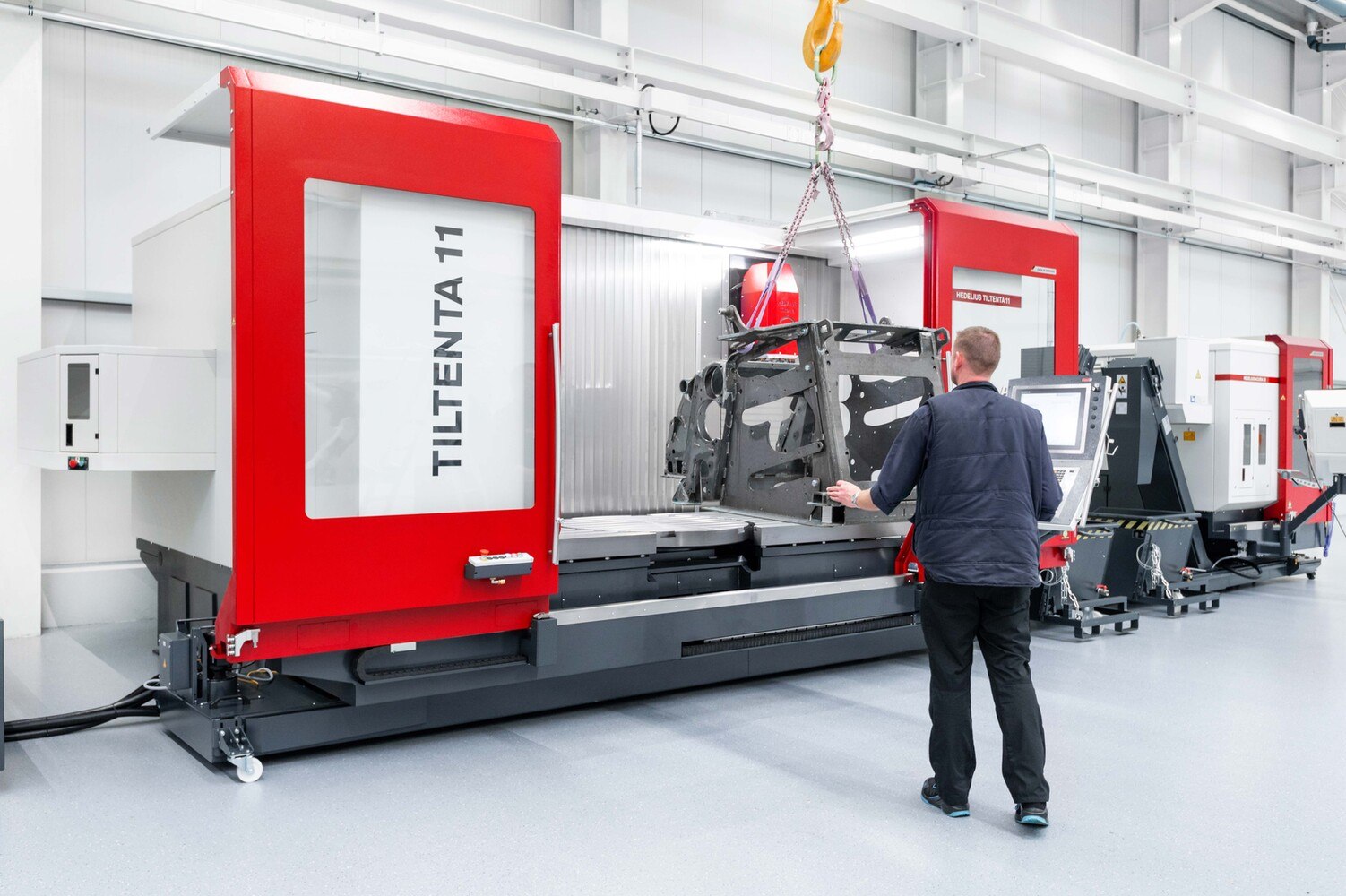
© HEDELIUS
Die Schwenkkopf-Fräsmaschine erscheint zunächst in zwei Varianten auf dem Markt, nämlich als T11-2600 mit entsprechendem X-Verfahrweg von 2.600 mm sowie als T11-3600 mit noch größeren X-Verfahrweg von 3.600 mm. Das vielseitig einsetzbare 4-Achs-Bearbeitungszentrum mit stufenlos schwenkbarer Hauptspindel kann durch den optionalen Einsatz eines Schwerlast-Rundtisches zum 5-Achs-Bearbeitungszentrum „hochgestuft“ werden, um noch flexibler zu fertigen. Mit einer Tischbelastung von maximal 4.000 Kilogramm auf dem Festtisch und 1.800 Kilogramm auf dem Rundtisch ist die Fertigung von massiven Großwerkstücken kein Problem. Nicht nur der Arbeitsraum, sondern vor allem auch die Verfahrwege können sich sehen lassen: Mit 2.600 x 1.100 x 900 mm (X, Y, Z) ist die Tiltenta 11-2600 für große Schweißkonstruktionen oder Grundplatten bestens geeignet, aber auch kleinere Bauteile können zu mehreren aufgespannt werden. Die Tiltenta 11-3600 bringt mit Verfahrwegen von 3.600 x 1.100 x 900 mm nochmal deutlich mehr Arbeitsraum in der X-Achse. Beide Bearbeitungszentren verfügen über 65 Werkzeugplätze im Standard und können darüber hinaus mithilfe eines Standby Magazins mit zusätzlichen 180 Werkzeugen auf insgesamt 245 Werkzeuge ausgerüstet werden.
HELLER: Viele Bearbeitungszyklen
Mit der neuen Generation der Baureihe F hat Heller vor Kurzem das 5-Achs-Bearbeitungszentrum F 6000 auf den Markt gebracht.
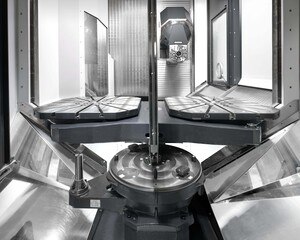
Das Ergebnis: gesteigerte Zerspanungsleistung und höhere Präzision, sowie zuverlässig bei einer 24/7-Produktion. Die F 6000 eignet sich für alle 5-Achs-Bearbeitung bis hin zur kombinierten Fräs-Dreh-Bearbeitung als Option, von Schwerzerspanung bis hin zur Bearbeitung von Leichtmetallen. Dabei kann der Anwender mit der Maschine ebenso effizient Einzel- wie auch Serienteile produzieren. Somit ist diese Werkzeugmaschine für unterschiedliche Branchen interessant – vom allgemeinen Maschinenbau über die Antriebs- und Energietechnik bis hin zu Aerospace. Durch eine Vielzahl an Optionen lässt sie sich optimal an den jeweiligen Kundenbedarf anpassen. Die Entwickler haben zahlreiche Verbesserungen erreicht.

© Südstahl Heller
Zu den Highlights zählen die grundlegend überarbeiteten Schwenkköpfe samt den darin integrierten und eigens von Heller entwickelten Motorspindeln. Die Speed Cutting Unit (SCU) erreicht in Verbindung mit Werkzeugschaft HSK-A 100 Drehzahlen von 15.000 U/min. Alternativ bietet Heller die für den universellen Einsatz ausgelegte Dynamic Cutting Unit (DCU) mit 380 Nm und 12.000 U/min. Für Schwerstbearbeitung steht weiterhin die Power Cutting Unit (PCU) mit einer Getriebespindel und 1.150 Nm zur Verfügung. Ebenso elementar ist das überarbeitete Antriebskonzept der Linearachsen mit zwei Kugelgewindetrieben in der Z-Achse und der deutlich verstärkten X-Achse. Sind neben komplexen Fräs- auch Dreharbeiten an Werkstücken gefordert, kann die Mill-Turn-Option der F 6000 für mehr Präzision und kürzere Produktionszeiten sorgen. Denn für das neue Bearbeitungszentrum steht ein schnelldrehender Rundtisch DDT (Direct Drive Turning) zur Verfügung. Er bietet hohes Drehmoment und erreicht Drehzahlen von bis zu 700 U/min. So lassen sich in einer Aufspannung ergänzend zu den herkömmlichen Fräs- und Bohroperationen auch Außen- und Innenkonturen im Drehverfahren bearbeiten. Die breite Auswahl an Bearbeitungszyklen deckt praktisch die Möglichkeiten einer konventionellen Drehmaschine ab.
HERMLE: Jede kann schwer zerspanen
In der Schwerzerspanung setzt Hermle vor allen Dingen auf die langjährige Erfahrung gerade im Werkzeug- und Formenbau, wo hohe Zerspanleistungen Tagesgeschäft sind. Generell können laut eigenen Aussagen alle Hermle-Maschinen in der Schwerzerspanung eingesetzt werden, wenn die richtige Spindelkonfiguration gewählt wird, am besten in einer Kombination mit 5-Achs-Anwendungen. Die Vorzeigemaschinen für die Schwerzerspanung sind die C 32 und C 62 aus der Baureihe High-Performance-Line. Beide sind mit hohen Spindelleistungen ausgestattet und mit ihren Drehmomenten und Leistungsdaten prädestiniert für die Schwerzerspanung. Bei Hermle sind alle Maschinen in modifizierter Gantry-Bauweise ausgeführt und bis zu einer gewissen Baugröße das Maschinenbett in Mineralguss. Gerade die Mineralgussausführung hat eine 6- bis 8-fach höhere Dämpfung als Stahlguss, was einer hohen Zerspanungsleistung zugutekommt. Die Mineralgussbetten werden in der eigenen Gießerei hergestellt, sodass das Know-how bereits im Haus ist. Eine weitere wichtige Komponente ist die Motorspindel der Maschine, von welcher die hohe Zerspanleistung im Wesentlichen beeinflusst wird. Hier spielen große Drehmomente und hohe Leistung eine zentrale Rolle. Natürlich sind hohe Zerspanleistungen nur mit optimal ausgelegten Werkzeugen in Kombination mit der jeweiligen Frässtrategie möglich. Hier findet ein reger Austausch zwischen Hermle und den jeweiligen Herstellern statt und im Einzelfall wird auch für Kunden getestet. //