Grenzen der Materialeigenschaften überwinden
Leicht wie Keramik und härter als Stahl: Ein neuer Werkstoff vereint die Vorteile beider Materialien für den Einsatz in Hochleistungsmaschinen.
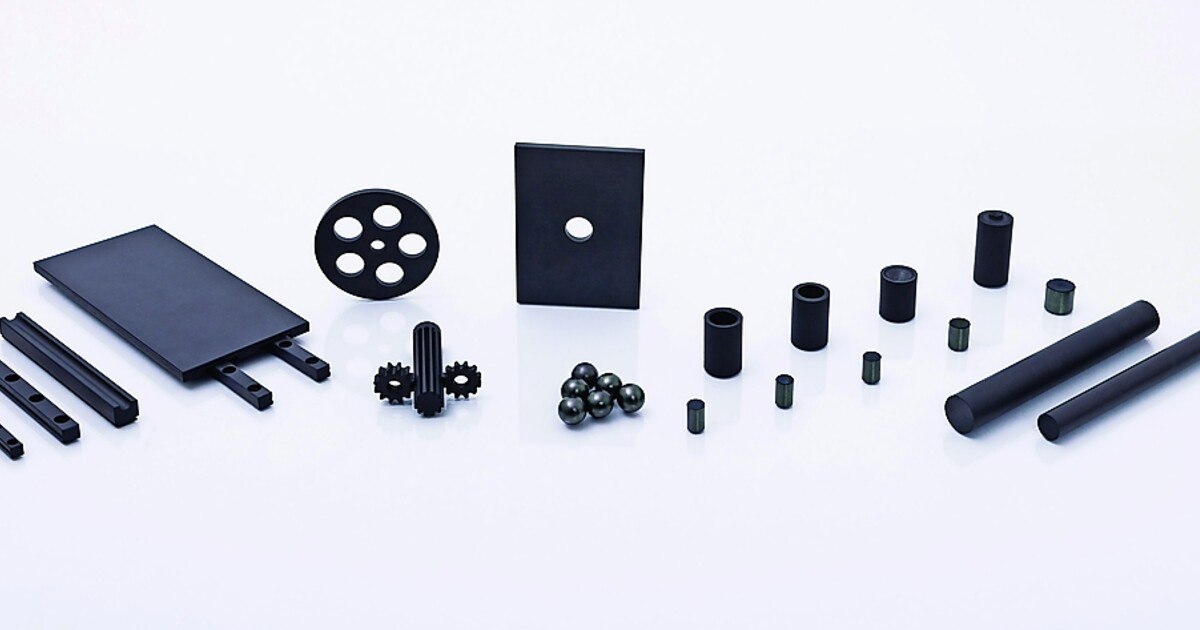
In der Metallbearbeitung sind Maschinenbauteile üblicherweise aus Stahl oder Keramik. Und beide Werkstoffe zeigen hier ihre Stärken und Schwächen. So eignet sich Stahl aufgrund seines Gewichts beispielsweise nicht für hohe Drehzahlen. Zudem korrodiert er vergleichsweise schnell, sofern er nicht mit einem entsprechenden, kostspieligen Schutz versehen wird. Keramische Komponenten wiederum gehen mit hohen Anschaffungskosten einher, die sich für viele Anwendungsbereiche kaum lohnen. Darüber hinaus lässt sich Keramik weniger gut mechanisch bearbeiten, was die Formgebung limitiert.
Der deutschen MLC Metal Like Ceramics GmbH scheint es nun gelungen zu sein, einen Werkstoff zu entwickeln, der die Vorteile von Stahl und Keramik vereint. Dank eines speziellen Herstellungsverfahrens könne das Unternehmen eigenen Angaben zufolge ein Ausgangsmaterial fertigen, das sich kostengünstig mit Extrusions- oder Spritzgussverfahren formen lässt. Durch eine anschließende Wärmebehandlung verwandle sich das Werkstück in ein leichtes Keramikprodukt, das Stahl in puncto Temperatur-, Korrosions- und Verschleißbeständigkeit übertreffe.
Jede Maschinenumgebung stellt unterschiedliche Anforderungen an die Materialien. Während Stahl für seine leichte Bearbeitbarkeit geschätzt wird, ist er ohne teure Speziallegierungen in korrosionsgefährdeten Bereichen weniger geeignet. Auch sehr hohe Drehzahlen sind mit dem schweren Werkstoff nur eingeschränkt möglich. Generell erhöhen harsche Umgebungen wie Korrosion die Ermüdung des Materials durch eine Schädigung des Materialgefüges. “Dort, wo Stahllager an ihre Grenzen kommen, wird üblicherweise auf Hybridlager oder auch vollkeramische Lager zurückgegriffen”, weiß Dr. Michael Schubert, Leiter der Produkt- und Prozessentwicklung bei MLC. Gegenüber den anderen Lagerarten böten keramische Lager Vorteile in Bezug auf Verschleiß-, Korrosions- und Temperaturbeständigkeit bei anspruchsvollen Anwendungsarten. Allerdings verbunden mit höheren Anschaffungskosten, die sich nicht für jede Situation rechtfertigen ließen, erklärt Schubert weiter. Deshalb müssten Maschinenhersteller stets verschiedene Lagertypen bereithalten, die je nach Maschinendesign und späterem Einsatzort entsprechend verbaut würden.
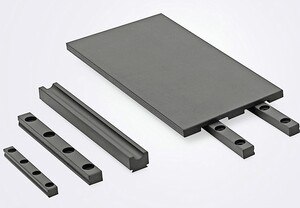
Der neue Werkstoff von MLC soll nun die jeweiligen Vorteile von Stahl und Keramik zusammenführen. Das Material sei im Vergleich zu Stahl robuster, gewichtsreduziert und verschleißbeständiger, lasse sich aber im Rahmen der Herstellung und Formgebung leichter bearbeiten als herkömmliche Keramik. Damit stehe ein “universaler Werkstoff” für die Herstellung zahlreicher Lager- und Komponentenvarianten bereit, bei allerdings deutlich geringeren Produktions- und Anschaffungskosten als klassische Hybrid- und Vollkeramiken aus Standardkeramiken wie z.B. SiN.
Die guten Materialeigenschaften ergeben sich laut MLC durch die patentierte Materialmischung. Das spezielle Herstellungsverfahren wiederum erlaube eine hohe Designfreiheit und vergleichsweise niedrige Kosten für die eigene Produktion.
“Bei der klassischen Keramikherstellung erfolgt eine aufwändige Produktion durch die eingesetzte Pulvertechnologie, die nur begrenzte Möglichkeiten in der Geometrie- und Formgebung bietet, sodass nachfolgende Sinterprozesse erforderlich sind”. Die Grünkörperfertigung werde so zu einem relativ teuren Produktionsschritt, sodass der Einsatz vollkeramischer Bauteile wohl überlegt werden müsse, erklärt Dr. Schubert.
Der “MLC“-Werkstoff hingegen werde in einem ersten Schritt aus einem polymeren Grundmaterial hergestellt, das mit aktiven und passiven Füllstoffen angereichert wird. Diese Masse kann dann durch bewährte Verfahren der Kunststoffindustrie, wie z. B. Extrusion oder Spritzguss, kostengünstig verarbeitet und in eine erste Vorform gebracht werden. Das polymere Material dient dabei als plastisches Matrixmaterial für die Füllstoffe.
Mithilfe einer ersten Wärmebehandlung wird die Vorform in einen bearbeitbaren Grünkörper verwandelt. Dieser besitzt eine plexiglasähnliche Beschaffenheit, wodurch ein endkonturnahes Bauteil mit nur geringem maschinellem Aufwand herausgearbeitet werden kann. Durch diese leichte Bearbeitung lassen sich nahezu alle gewünschten Geometrien realisieren, und der Werkzeugverschleiß ist im Vergleich zur Bearbeitung anderer Werkstoffe äußerst gering. Zum Abschluss wird das aus dem Grünkörper geformte Bauteil in einem Hochtemperaturschritt final gefestigt, wodurch es seine stahlähnliche Härte von 1000 HV bekommt. Dabei wird das Silikonharz vollständig umgesetzt und Rückstände bleiben aus. Für hochgenaue Bauteile kann das keramische Material deshalb ohne großen Aufwand und den Einsatz teurer Werkzeuge wie Diamantschleifer nachbearbeitet werden.
MLC eigne sich laut Hersteller für Anwendungen in den verschiedensten Branchen. Etwa für Bauteile im Reinraum und Vakuum, aber auch für korrosive oder verschmutzte Umgebungen, in denen schlechte Schmierbedingungen herrschen. Dabei zeige sich das Material laut Dr. Schubert auch unempfindlich gegenüber Temperaturschwankungen. Wegen der flexiblen Formgebung sei auch der Einsatz jenseits reiner Lager- und Antriebskomponenten denkbar. Etwa in Elektronik, Mechatronik, Leichtbau, Medizintechnik oder auch in kunststoffverarbeitenden Betrieben.
“Wir sind kontinuierlich dabei, das Material mit Partnern weiterzuentwickeln, um neue Einsatzgebiete wie die Verarbeitung im 3D-Druck zu ermöglichen”, so Schubert. [gr]