Nachhaltige Baumaschinen
Elektrifizierung - Herzstück auf dem Weg zu null Emission
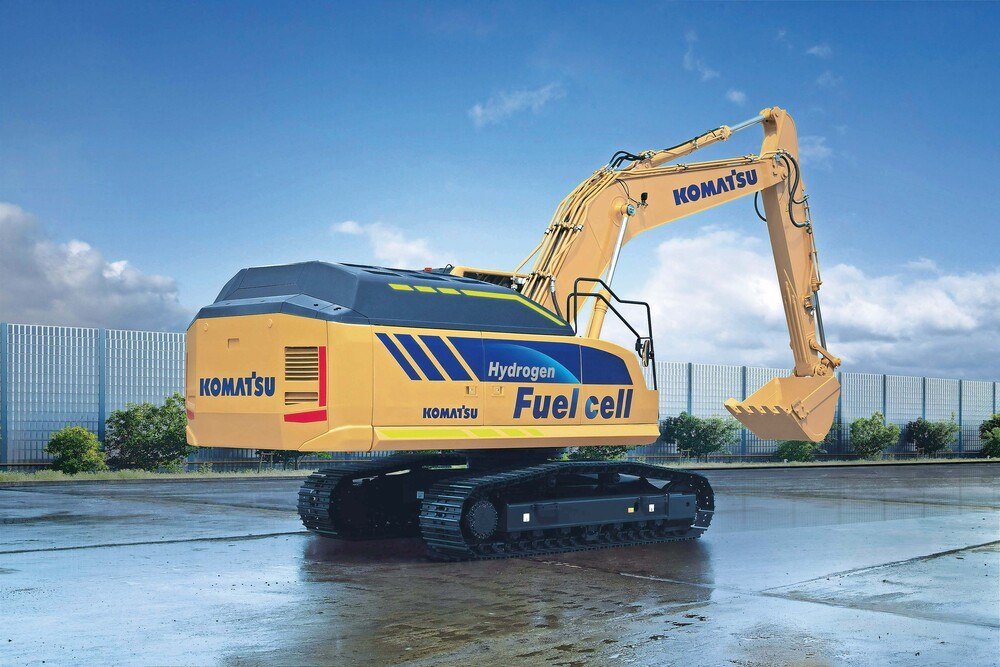
Nicht nur Leistung und Effizienz von Baumaschinen sind in den letzten Jahren enorm gesteigert worden, auch die digitale Revolution hat die Baubranche – und damit den Bereich der Bagger – mittlerweile erfasst. Moderne Bagger sind heute mit einer beeindruckenden Palette von Technologien ausgestattet. „Generell ist der Anteil der Projekte, bei denen eine 2D- oder 3D-Maschinensteuerung erforderlich ist, gestiegen“, erklärt beispielsweise Gerhard Thir, Geschäftsführer des auf Transport und Erdbau spezialisierten Unternehmens Thir. „Wir haben daher vor zwei Jahren einen Cat 320 auf 3D-Steuerung aufgerüstet und beschäftigen einen eigenen Vermessungstechniker. Auch zwei unserer drei Grader sind bereits mit der 3D-Technik ausgerüstet. In unserem Fuhrpark spielen Cat-Geräte seit rund 50 Jahren eine wichtige Rolle, daher haben wir uns bei der jüngsten Investition für zwei neue Cat-Kurzheckbagger entschieden. Der Cat 315 und der Cat 325 sind Vertreter der aktuellsten Gerätegeneration und verfügen bereits ab Werk über eine umfangreiche Ausstattung mit verschiedenen Assistenzsystemen.“
„Eine vollwertige Maschinensteuerung wird in Zukunft Teil der Basisausrüstung einer Baumaschine sein“, ergänzt Wolfgang Grün vom Baumaschinenspezialisten Zeppelin. „Daher ist die Arbeit mit der 2D-Steuerung, wie sie bei den Next-Generation-Geräten serienmäßig verfügbar ist, vor allem für junge Fahrer ein guter Einstieg. So werden sie mit dieser Technik vertraut und sind später mit einer 3D-Steuerung nicht überfordert.“
Maschine passt sich an Fahrer an
Zu den Stärken der Next-Generation-Geräte würde neben den integrierten Assistenten aber auch die Möglichkeit, die Belegung der Joysticks oder die Geschwindigkeiten von Stiel- und Löffelzylinder auf die eigene Arbeitsweise anzupassen, zählen. „Dadurch passt sich das Gerät dem Fahrer an und nicht umgekehrt. Ein weiteres Assistenzsystem ist die Systemfunktion E-Fence, die etwa bei Straßenbaustellen den Arbeits- und Schwenkbereich begrenzt. Weiters unterstützt die Cat-Payload-Technologie den Fahrer dabei, eine Über- oder Unterladung zu vermeiden und die Effizienz zu maximieren.“
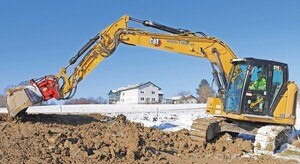
Während der Cat 315 von Zeppelin als Allround-Gerät sowohl im Erdbau als auch im Abbruch zum Einsatz komme, liege der Schwerpunkt beim Cat 325 überwiegend im Forstwegebau. Hier sei die serienmäßige 2D-Steuerung für die Herstellung der entsprechenden Gefälle ausreichend. Damit der Cat 325 für die teilweise sehr schwierigen Einsätze optimal ausgerüstet ist, wurde er mit einem OilQuick-Schnellwechsler OQ70/55 und einem Böschungslöffel mit Drehmotor ausgerüstet.
Herstellerübergreifend haben mittlerweile verschiedenste Technologien Einzug gehalten, etwa die GPS-Steuerung. Durch die Integration von GPS-Systemen können Baggerführer heute präzise und wiederholbare Grabeinsätze durchführen. Dies reduziert menschliche Fehler und beschleunigt den Fortschritt komplexer Projekte. Daneben erfassen und analysieren Telematiksysteme die Betriebsdaten in Echtzeit. Maschinelles Lernen hilft wiederum vielfach dabei, den Wartungsbedarf vorherzusagen und Ausfallzeiten zu minimieren.
Kollisionsvermeidungssysteme nutzen zudem Sensoren und Kameras, um Baggerführer vor potenziellen Kollisionen mit Hindernissen oder anderen Maschinen zu warnen, wodurch die Sicherheit erheblich erhöht wird.
Schnittstelle Mensch/Maschine
So stand etwa bei der Entwicklung des Mobilbaggers EW100 von Wacker Neuson die Baustelle 4.0 im Fokus, herausgekommen ist dabei unter anderem ein intelligentes Attachment-Management, ein durchdachtes Human-Machine-Interface und die Vorbereitung für diverse Assistenzsysteme und Schnittstellen. Die Maschine kann laut dem Hersteller den Bediener beim Anbaugerätewechsel über das integrierte Zehn-Zoll-Display unterstützen, etwa indem die Maschinendynamik automatisch an das angebaute Werkzeug angepasst werde. Außerdem punkte der Bagger Wacker Neuson zufolge im Bereich Sicherheit durch gute Sichtverhältnisse und eine hohe Standsicherheit, auch bei einer 360-Grad-Drehung mit gehobener Last. Verständlicherweise standen weiterhin bei der Entwicklung des Baggers vor allem auch Bedienerfreundlichkeit und Effizienz im Mittelpunkt, so könnten durch die leistungsstarke Fahrhydraulik und die hohe Grundarbeitsleistung mit der Maschine auch Aufgaben erledigt werden, für die sonst ein 14-Tonnen-Bagger eingesetzt werden müsste.
Auch die Elektrifizierung hat in den letzten Jahren erheblich an Bedeutung gewonnen, da sie die Umweltauswirkungen der Baubranche reduziert und gleichzeitig betriebliche Vorteile bietet. Die Umstellung von Verbrennungsmotoren auf elektrische Antriebe erfolge zwar nicht von heute auf morgen, aber die Dynamik wachse und die EMEA-Region sei dabei führend, wie Cédric Durand, Director Product Management EMEA bei Yanmar CE, erläutert. Yanmar ist vor allem für die Erfindung des kleinen Dieselmotors im Jahr 1933 bekannt, heute übernimmt das Unternehmen aber eine Vorreiterrolle dabei, Verbrenner durch neue Konzepte zu ersetzen. Das Unternehmen will noch im heurigen Jahr mit der Auslieferung seines ersten emissionsfreien Minibaggers SV17e sowie des Kompaktradladers V8e in Europa beginnen. Heute, „wo die Emissionen von Verbrennungsmotoren das Klima belasten“, sei klar, dass zur Verbesserung der Gesellschaft neue Lösungen erforderlich sind. Der Einsatz von elektrischem Strom sei dabei ein wichtiger Schritt.
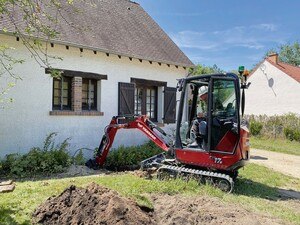
Die Einführung des SV17e und des V8e seien dabei wichtige strategische Schritte im Rahmen der zukünftigen Transformation von Yanmar CE. Mit einer Batteriekapazität von 23,5 kWh beziehungsweise 40 kWh (und einer 52 kWh-Option) seien die Maschinen leistungsfähig, kraftvoll und hochproduktiv – und würden dabei die strengsten Emissionsvorschriften der Welt erfüllen. So gut die Maschinen auch sind, die neue Generation von Elektromaschinen habe Schwierigkeiten, sich durchzusetzen, wie Durand erklärt. Die Technologie sei neu und die Kund*innen würden vor dem großen Umstieg zurückschrecken. Zudem sei der Anschaffungspreis von Elektromaschinen aufgrund der hohen Komponentenpreise höher als jener vergleichbarer ICE-Maschinen. Auch die Ladeinfrastruktur stecke noch in den Kinderschuhen, neue Maschinen würden überdies eine andere Arbeitsweise erfordern, auch die Restwerte seien bislang unbekannt. Dennoch, trotz dieser Herausforderungen führe kein Weg an der Elektrifizierung der Branche vorbei – und dieser Wandel werde zuerst in Europa stattfinden.
Kund*innen brauchen Auswahl an Elektromaschinen
„Es wird nicht einfach sein, aber bis 2050 wollen wir Netto-Null-Emissionen erreichen“, so Durand. „Nicht nur Yanmar, sondern auch die Kund*innen von Yanmar. Wir folgen einer Roadmap, um dies zu erreichen – und die Elektrifizierung ist das Herzstück davon. Kund*innen und Länder zeigen Interesse – das ist ein wichtiger erster Schritt.“ So würden sich beispielsweise große Vermieter an den Markt herantasten, ebenso seien mehrere große Bauunternehmen mit ESG-Zielen in diesem Bereich engagiert. „Skandinavien und die nordischen Länder, insbesondere Norwegen, sind führend auf dem Gebiet der Emissionsfreiheit, jedoch sind dies noch kleine Märkte. Damit die Absatzmengen wirklich wachsen und die Kosten durch Skaleneffekte gesenkt werden können, brauchen wir eine große europäische Wirtschaftsnation wie Deutschland, Frankreich oder das Vereinigte Königreich, um die Elektrifizierung voranzutreiben. Das ist noch nicht der Fall. Aber wenn es so weit ist, glauben wir daran, dass es schnell gehen wird – und wir müssen eine Auswahl von Elektromaschinen parat haben.“
Die Verschärfung der Umweltvorschriften und die Einrichtung von Umweltzonen mit extrem niedrigen (oder gar keinen) Emissionen in städtischen Gebieten würden ebenso dazu beitragen, die Umstellung auf elektrische Maschinen zu beschleunigen. „Das Gleiche gilt für die Betriebskosten. Es kostet weit weniger, eine Maschine mit Strom aufzuladen, als sie mit Diesel zu betanken.“ Zusätzlich würden weniger Wartungsteile (wie Öl und Ölfilter) benötigt. Diese Kombination könnte durchaus dazu führen, dass die Gesamtbetriebskosten von Elektromaschinen niedriger seien als die von Dieselfahrzeugen – selbst bei einem höheren Anschaffungspreis.
Ein gravierendes Problem sei allerdings die Lebensdauer der Batterien. „Bei den Produkten, die wir in diesem Jahr auf den Markt bringen, wird die Lebensdauer der Batterien mindestens der einer Dieselmaschine entsprechen“, verspricht Durand. „Wir arbeiten auch an Möglichkeiten zur Wiederverwendung von Altbatterien, um einen Beitrag zur Kreislaufwirtschaft zu leisten.“
Der Hersteller arbeite eng mit den eigenen Händlern zusammen, um sicherzustellen, dass Kund*innen „denselben hervorragenden Service“ erhalten, den sie gewohnt seien. „Abgesehen von der Frage der Nachhaltigkeit ist die Elektrifizierung in Bezug auf Leistung, Fahrerkomfort und Wirtschaftlichkeit der richtige Weg. Wir stellen die Kund*innen in den Mittelpunkt unseres Handelns und streben zumindest an, dass unsere elektrischen Maschinen der ersten Generation einfach zu bedienen sind und eine ähnliche Leistung aufweisen wie unsere vergleichbaren dieselbetriebenen Maschinen.“ In den letzten 50 Jahren habe es keine so große Veränderung gegeben: „Wir werden uns alle anpassen und Kompromisse eingehen müssen, aber die Elektrifizierung wird kommen. Das ist gut für das Klima und gut für die Wirtschaft – es ist eine spannende Aussicht.“
Wasserstoff tanken
Dies sehen auch andere Hersteller so, zum Beispiel Komatsu. Das Unternehmen hat jüngst einen mittelgroßen Konzept-Hydraulikbagger entwickelt, der eine Wasserstoff-Brennstoffzelle sowie weitere, von Komatsu entwickelte, zentrale Komponenten vereine, um CO₂-Neutralität auf Baustellen zu erreichen. Mit dem Start der Machbarkeitsstudie im Mai 2023 beschleunigte das Unternehmen laut eigenen Angaben das eigene Vorhaben der kommerziellen Herstellung von mittelgroßen und großen Baumaschinen mit Wasserstoff-Brennstoffzellen in naher Zukunft.
In einem mittelfristigen Managementplan hat sich Komatsu die Reduzierung von Umweltauswirkungen im gesamten Unternehmen zum Ziel gesetzt. CO₂-Emissionen aus der Herstellung und Nutzung der Baumaschinen sollen in dessen Rahmen bis 2030 um 50 Prozent reduziert werden (im Vergleich zum Niveau von 2010, Anm. d. Red.). Bis 2050 soll beides CO₂-neutral sein. Damit auch die Kund*innen des Unternehmen CO₂-Neutralität erreichen können, werden verschiedenste Produkte, Dienstleistungen und Lösungen geboten. Zudem forscht der Hersteller an Maschinen mit gänzlich neuen Energiequellen.
Für die Konzeptmaschine wird ein Wasserstoff-Brennstoffzellen-System ebenso wie ein Wasserstofftank der Toyota Motor Corporation in einem mittelgroßen Hydraulikbagger genutzt. Durch die Verbindung der hochentwickelten Steuerung und zentralen Komponenten von Komatsu mit dem Brennstoffzellensystem von Toyota sei mit einer deutlichen Reduzierung des Vibrations- und Geräuschpegels bei gleicher Grableistung und Bedienbarkeit wie bei Baggern mit Verbrennungsmotor zu rechnen, verspricht der Hersteller.
Gleiche Leistung wie Verbrennermodelle
Daneben kündigte Komatsu Europe unlängst auch den PC33E-6 an, einen elektrischen Drei-Tonnen-Minibagger mit Lithium-Ionen-Batterie. Dieser soll neue Maßstäbe, was emissionsfreies Arbeiten angeht, setzen und biete herausragende Leistung und verschiedene Sicherheitsfunktionen. Der PC33E-6 beruhe auf mehr als einem Jahrhundert Know-how in Design, Entwicklung und Fertigung bei Komatsu und unterstreiche das Engagement des Unternehmens für eine nachhaltige Zukunft.
So könne der Minibagger im Vergleich zu konventionellen dieselbetriebenen Maschinen jährlich mehr CO₂-Emissionen einsparen, als er selbst wiegt – ohne Kompromisse bei Leistung und Sicherheit einzugehen, wie Emanuele Viel, Group Manager Utility bei Komatsu, betont. „Der PC33E-6 verfügt über Batterien mit großer Kapazität und über einen hocheffizienten Antriebsstrang, der es den meisten Kund*innen ermöglicht, eine ganze Schicht lang ununterbrochen ohne Laden zu arbeiten. Dank des blitzschnellen Ladesystems werden die Ausfallzeiten erheblich reduziert, was die Produktivität und Effizienz auf der Baustelle erhöht.“
Auch Volco CE setzt auf Elektroantriebe, so ist seit kurzem der erste mittelgroße Elektrobagger für ausgewählte Kund*innen in Deutschland, der Schweiz und weiteren europäischen Ländern erhältlich. Mittelgroße batterieelektrische Bagger seien in der Baubranche noch Mangelware, erläutert Thomas Bitter, Head of Technology bei Volvo CE. Eine Ausnahme bilde dabei der Volvo EC230, der sich bereits in etlichen Anwendungen bewährt habe. Der 23-Tonnen-Elektrobagger biete die gleiche Leistung wie ein vergleichbares Dieselmodell, sei dabei allerdings emissionsfrei, geräusch- und vibrationsarm. Zudem werde eine ähnliche Grabkraft wie beim Dieselpendant Volvo EC220E erreicht, und dies mit einer schnelleren Zykluszeit und deutlich weniger Lärm kombiniert.
Die Vorteile bezüglich Lärm- und Schadstoffemissionen habe der Elektrobagger dabei bereits in etlichen Großprojekten unter Beweis gestellt, etwa bei der Umgestaltung des alten Schlachthofareals in Stockholm. „Wenn ich in dieser Größenklasse die Wahl zwischen einer elektrischen oder einer Dieselmaschine hätte, würde ich mich für die elektrische Maschine entscheiden. Sie bietet so viele Vorteile! Anfangs gab es zahlreiche Skeptiker, die meinten, die Maschine hätte nicht die Kapazität für einen kompletten Arbeitstag – aber sie wurden alle eines Besseren belehrt“, erklärt beispielsweise Richard Sjöblom, Baggerfahrer im Rahmen des Schlachthof-Projekts, nach dem Testeinsatz.
Allzweckmaschinen für den elektrischen Arbeitstag
Der Antrieb des Baggers werde von Lithium-Ionen-Batterien gespeist und sei mit einer schnellen Zwischenladung für einen vollen achtstündigen Arbeitstag ausgelegt, betont Bitter. Als Allzweckmaschine biete sich der EC230 Electric für eine Vielzahl von Aufgaben an, darunter Extraktion, Erdbewegung, Planierung sowie Abfall- und Schrottumschlag im Recycling- und Abfallsegment. Die Erkenntnisse aus dem Einsatz des EC230 Electric will Volvo CE zur Entwicklung weiterer Elektromodelle nutzen – „immer auch in enger Abstimmung mit Zulieferern und Kunden“. Dieser partnerschaftliche Ansatz ermögliche eine umso zügigere Markteinführung, wobei Volvo CE ein ehrgeiziges Ziel nicht aus dem Auge verliert: eine Nettonull bei den Treibhausgasemissionen bis zum Jahr 2040. „Die Partnerschaft mit unseren Kund*innen ist ein wichtiger Teil unserer Innovationsreise. Durch die enge Zusammenarbeit erhalten wir wertvolles Feedback, um unser Angebot kontinuierlich zu verbessern und nachhaltige Lösungen zu entwickeln“, erklärt Bitter.
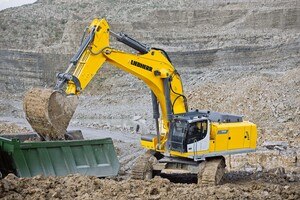
Liebherr setzt indes darauf, auch bestehende Verbrennerkonzepte effizienter zu machen. So ersetzen die jüngst präsentierten Modelle der Raupenbagger R 972, R 978 SME, R 992 und R 998 SME die bestehenden Modelle R 966, R 970 SME, R 976 und R 980 SME. Die 70- bis 100-Tonnen-Raupenbagger sollen sich durch zahlreiche Verbesserungen wie beispielsweise optimierte Leistungsdaten, hoher Komfort, neue Assistenzsysteme und reduzierter Kraftstoffverbrauch auszeichnen. Die Benennung stehe dabei in direktem Zusammenhang mit dem Einsatzgewicht der Maschinen. Eine Modernisierung der Designsprache begleite die Umbenennung und betone auch die Verwandtschaft zur Generation 8.
Der R 992 wurde beispielsweise mit dem Ziel einer Reduktion des Gesamtenergieverbrauchs entwickelt, eine wichtige Rolle spiele dabei das patentierte System „Liebherr Power Efficiency (PE) – Engine Control“. Die PE-Funktion komme zu den bereits bestehenden Arbeitsmodi der Maschine (P+/P/E) hinzu und erlaube eine Verringerung des Kraftstoffverbrauchs von zehn bis 15 Prozent gegenüber den Vorgängermodellen. Der R 992 sei auch mit der sogenannten Bucket-Fill-Assist-Assistenzfunktion erhältlich, ein Anti-Stalling-Modus verhindere ein Blockieren des Löffels während der Eindringphase in das Grabgut und biete zusätzliche Unterstützung des Fahrers für eine höhere Produktivität und mehr Komfort. Die Funktion zur automatischen Befüllung des Löffels biete darüber hinaus einen automatisierten Zyklus für eine schnellere Löffelbefüllung.