Neue Technik
Schweißverfahren EHLA: Wie es funktioniert und was es bringt

Herkömmliche Bremsscheiben bestehen aus Gusseisen mit eingelagertem Graphit, das sich durch eine gute Temperaturleitfähigkeit und ein gutes Wärmespeichervermögen bei gleichzeitig geringem Preis auszeichnet. Korrosionsneigung und hoher Materialverschleiß im Betrieb führen allerdings zu beträchtlichen Feinstaubemissionen. Übliche Beschichtungsprozesse - etwa galvanotechnische Verfahren oder thermisches Spritzen -können die Bremsscheiben bislang nicht effektiv schützen. Denn sie ermöglichen keine stoffschlüssige Verbindung der Schutzschichten mit dem Gusseisen und sind material- und kostenintensiv.
Die Vorteile des EHLA-Verfahrens
Mit dem neuen EHLA-Verfahren (Extremes Hochgeschwindigkeits-Laserauftragschweißen) lassen sich erstmals gut haftende Schichten auf Bremsscheiben auftragen, die fest mit dem Grundstoff verbunden sind und nicht abplatzen können.
Das EHLA-Verfahren wurde vom Fraunhofer-Institut für Lasertechnik ILT in Aachen gemeinsam mit dem Lehrstuhl Digital Additive Production DAP der RWTH Aachen University entwickelt. Mittels EHLA erzeugte Schichten sind dicht und haben keine Poren oder Risse. Dies erhöht die Lebensdauer der Beschichtung und verhindert frühzeitige Ausfälle durch Oberflächenschäden der Reibflächen. Da eine große Materialpalette verarbeitet werden kann, wird eine anwendungsangepasste Beschichtung mit umweltfreundlichen Materialien möglich.
Die Innovation basiert auf dem bereits bekannten Laserauftragschweißen, das sich als Reparaturverfahren etwa für Turbinenschaufeln bewährt hat. Beim EHLA-Verfahren werden allerdings die Pulverpartikel des Beschichtungswerkstoffes direkt im Laserstrahl aufgeschmolzen und nicht erst im Schmelzbad auf der Oberfläche des Bauteils. Da so flüssige Materialtropfen statt feste Pulverpartikel in das Schmelzbad gelangen, kann die Prozessgeschwindigkeit von bisher 0,5 bis 2 Metern pro Minute beim herkömmlichen Laserauftragschweißen um mehrere Größenordnungen auf bis zu 500 Meter pro Minute gesteigert werden.
Die große Prozessgeschwindigkeit führt dazu, dass die Wärmeeinwirkung auf das zu beschichtende Material deutlich sinkt. Statt wie beim herkömmlichen Laserauftragschweißen bis in den Millimeterbereich wird durch EHLA das Material nur im Mikrometerbereich thermisch beeinflusst. So werden auch neue Materialkombinationen möglich - etwa die Beschichtungen von Aluminium- oder Gusseisenlegierungen, wie nun bei den Bremsscheiben.
Anders als bei herkömmlichen Auftragschweißverfahren wird mit EHLA vermieden, dass sich der Kohlenstoff aus der Bremsscheibe in der Schmelze löst, wodurch sonst spröde Phasen, Poren, Bindefehler und Risse in der Beschichtung bzw. der Anbindungszone entstehen. Damit können Bremsscheiben aus Grauguss erstmalig effektiv mit stoffschlüssig angebundenen Schichten geschützt werden.
Ressourceneffizientes Schweißverfahren
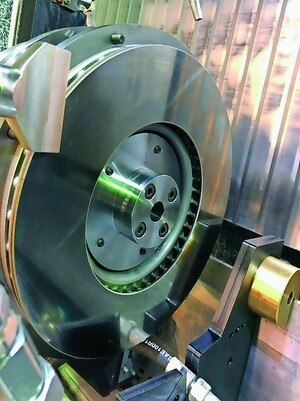
Normalerweise können mit Auftragschweißverfahren nur dicke Schichten ab einem halben Millimeter hergestellt werden. Das mittlerweile schon mit drei Innovationspreisen ausgezeichnete EHLA-Verfahren ermöglicht nun, auch sehr dünne Schichten mit Dicken von 25 bis 250 Mikrometern aufzutragen. Die Schicht wird reiner und glatter - die Rauheit konnte auf etwa ein Zehntel bisheriger Werte reduziert werden. Außerdem werden beim Verfahren rund 90 Prozent des Materials genutzt. Dadurch ist EHLA ressourcenschonend und wirtschaftlich. Eine serientaugliche Anlagentechnik mit angepasster Endbearbeitung durch Schleifen wird gerade in Aachen durch die Firma HPL Technologies aufgebaut.
[Quelle: METALL 12/2019]