Kompressoren
Viel Luft mit wenig Energie

Als Metallbauer will man sich auf sein Kerngeschäft konzentrieren – nicht auf die Druckluftversorgung. Die muss zuverlässig im Betrieb zur Verfügung stehen. Daher gibt es Spezialisten wie Atlas Copco, Boge oder Kaeser, die neue effiziente Druckluftanlagen installieren oder bestehende genau durchleuchten und Einsparungspotenziale „aufspüren“.
Was kostet Druckluft?
Druckluft ist ein sehr teurer Energieträger: Von der zur Erzeugung aufgewendeten elektrischen Energie bleiben am Ende weniger als zehn Prozent Nutzenergie übrig. Die Kosten für die Drucklufterzeugung setzen sich vorwiegend aus drei Faktoren zusammen: den Investitionskosten für die Maschine, den Wartungs- und Instandhaltungskosten im laufenden Betrieb sowie den Energiekosten, um den Kompressor anzutreiben. Über die gesamte Lebenszeit eines Kompressors stellen diese Energiekosten den Löwenanteil der Gesamtkosten für die Drucklufterzeugung, meistens 70 bis 80 Prozent. Je nach den jährlichen Betriebsstunden, Nutzungsgrad und dem aktuellen (derzeit hohen) Energiepreis rechnet sich die Investition in eine energieeffiziente Druckluftversorgung in meistens zwei bis drei Jahren – allein durch die eingesparte Energie.
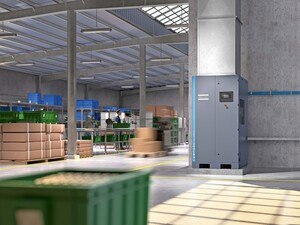
Bedarf ist eine Auslegungssache
Bei neuen Anlagen ist die kluge Planung des Druckluftnetzes wesentlich. Ein falsch dimensioniertes Druckluftsystem zieht schnell gravierende Folgekosten nach sich, deshalb steht am Beginn die möglichst genaue Analyse des geplanten Druckluftbedarfs. Dabei helfen auch die renommierten Anbieter wie Atlas Copco, Boge, Kaeser mit ihren Berechnungs-Tools. Die benötigte Druckluftmenge bezieht sich auf die Summer aller Entnahmestellen. Zu bedenken gilt es, wie viele Verbraucher abwechselnd oder gleichzeitig betrieben werden. Und welchen maximalen Betriebsdruck der größte Abnehmer braucht.
Kosten sparen, Effizienz steigern
Für diesem Bericht haben wir Tipps zur Kostensenkung und Verbesserung der Energieeffizienz in einem Druckluftsystem „aufgespürt“. Die genannten Maßnahmen und Einsparungen basieren auf den Erfahrungen der oben genannten Anbieter und weichen manchmal voneinander ab oder weisen eine größere Bandbreite auf. Welche Maßnahmen wie schnell wirken und sich rechnen, ist unterschiedlich. Grundsätzlich gilt es, alle Verbraucher im Betrieb bedarfsorientiert zu optimieren, Energieverluste zu vermeiden sowie vorhandene Ressourcen aufzuspüren. „Greifen“ diese Maßnahmen nicht, kann auch eine technologische Modernisierung notwendig sein.
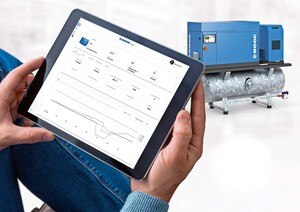
Die Qual der Wahl
Für Betriebe, die in ihrer Produktion viel Druckluft benötigen, beginnt das Energiesparen bereits bei der Auswahl eines effizient arbeitenden Kompressors. Angeboten werden viele Modelle. Doch nicht jeder Kompressor eignet sich gleichermaßen für alle Einsätze, sondern es gibt für jede individuelle Anforderung im Hinblick auf Druck, Volumen, Einsatzhäufigkeit oder Bedarfsschwankung die passende Druckluftlösung.
Für Anwender wie auch Anbieter ist heute die Energieeffizienz der Kompressoren der wesentliche Faktor, vor allem bei einem hohem und schwankendem Druckluftbedarf. Dafür empfehlen sich drehzahlgeregelte Schraubenkompressoren der neuesten Generation. Diese sind zwar nicht billig, doch die höhere Investition zahlt sich relativ flott aus. Der Idealfall, dass ein einzelner Kompressor den gesamten Druckluftbedarf abdeckt, kommt zwar vor. Doch wenn, wie oft in Metallbaubetrieben, sehr viel Druckluft benötigt wird, bedarf es mehrerer Kompressoren. Wird dazu ein übergeordnetes (dezentrales) Druckluftmanagementsystem eingesetzt, kann die gesamte Anlage je nach Volumen bedarfsgerecht und effizient ausgelastet werden, was den Energieverbrauch insgesamt deutlich reduziert.
Drehzahlgerechte Kompressoren
Kompressoren mit variabler Drehzahl passen die Drucklufterzeugung dem jeweiligen Bedarf an. Das bedeutet, der Motor läuft nur mit jener Geschwindigkeit, die gerade erforderlich ist, um den aktuellen Druckluftbedarf zu bedienen. Diese Regelung ist sehr effizient, da der Luftbedarf in der Praxis selten durchgehend konstant ist. Es gibt oft produktionsintensivere Tage oder Schichten, am Abend oder Wochenende wird in vielen Betrieben die Produktion ganz heruntergefahren. Die einfachste Variante zum Energiesparen ist dann: den Kompressor bei Nichtgebrauch ausschalten und nicht „leer“ laufen lassen. Das kann die Energiekosten sogar um bis zu 80 Prozent senken.
Leckagen orten und beheben
Selbst wenn keine großen, zischenden Leckagen (undichte Stellen) vorhanden sind: Druckverluste kann man nicht gänzlich verhindern, ein Großteil der Kompressorleistung – das können „schlanke“ 15 bis zu 60 Prozent im Extremfall sein – geht auf dem Weg zum Verbraucher verloren. Dabei addieren sich besonders in älteren Leitungsnetzen viele kleine Leckageverluste wie beispielsweise nicht ordentlich verschraubte Leitungen, ineffiziente Kupplungen, defekte Schläuche oder undichte Ventile zu einem großen Problem, das dann richtig Geld kostet. Bereits ein kleines Leck von nur zwei Millimetern Durchmesser in der Druckluftverteilung führt zu erheblichen Luftverlusten und kostet mehrere Tausend Euro. Denn der Kompressor muss viel mehr Luft bereitstellen, als bei optimaler Auslegung des Netzes nötig wäre.
Das Einsparpotenzial ist selbst bei kleinen Betrieben beträchtlich. Eine pauschale Aussage darüber kann man allerdings nicht treffen, dazu sind die Situationen in den Betrieben zu unterschiedlich. Die Leckageverluste muss der Kompressor „ausgleichen“ und verbraucht dadurch natürlich deutlich mehr Strom. Besonders, wenn der Kompressor rund um die Uhr läuft (laufen muss). Daher sind regelmäßige Kontrollen des gesamten Druckluftsystems „Pflicht“. Diese Prüfungen sollte man am besten Fachleuten überlassen, die Leckagen professionell orten, beheben und das Leitungsnetz danach optimieren. Der Experte geht das komplette Rohrnetz im Betrieb ab – vom Kompressor bis zum kleinsten Druckluftverbraucher, scannt alle Rohre, Verbindungen und Ventile. Danach erhält man ein genormtes Druckluftaudit, was eine unabhängige Bewertung der Energieeffizienz des Druckluftsystems darstellt.
Wärmerückgewinnung nutzen
Druckluftanlagen erzeugen viel Wärme. Damit diese kostbare Energie nicht ungenützt verloren geht, ist es möglich, bis zu 90 Prozent der Wärme aus der erzeugten Druckluft zurückzugewinnen und sie energetisch sinnvoll nochmals zu „verwerten“. Dabei gibt es verschiedene Möglichkeiten, diese Abwärme im Betrieb zu nutzen: für die Heizung der Betriebsräume und Werkshallen, zum Erhitzen von Nutz- und Brauchwasser (bis zu 90 Grad C, etwa für Reinigungsvorgänge) oder als Prozesswärme in der Metallbearbeitung. Wie viel Wärme „kostenlos“ zurückgewonnen werden kann, hängt unter anderem von den Kompressoren, der Art ihrer Kühlung, dem Druckluftsystem und den Möglichkeiten ab, die Wärme im Betrieb zu nutzen. Über den wirtschaftlichen Aspekt hinaus lässt sich mit der „Zweitverwertung“ und der damit einhergehenden Einsparung von „frischem“ Strom auch die eigene CO2-Bilanz deutlich verbessern.
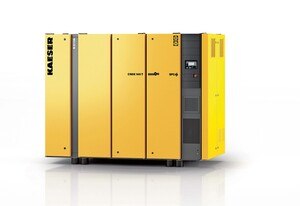
Die Anbieter und ihre Tools
Das Technologie-Portfolio der Anbieter Atlas Copco, Boge und Kaeser reicht von hocheffizienten drehzahlgeregelten Kompressoren über Systeme zur Wärmerückgewinnung und übergeordnete Steuerungen bis hin zu Tools zum Analysieren und Berechnen eines vorhandenen wie auch neuen Druckluftsystems.
Enorm sparsam
Atlas Copco bietet sehr energieeffiziente Schraubenkompressoren (GA VSDS) mit variablem Drehzahlantrieb (VSD), die bis zu 60 Prozent Energie einsparen, indem sie ihre Motordrehzahl an die Schwankungen des Druckluftbedarfs anpassen. Mit einem Schallpegel von nur 63 dB benötigt zum Beispiel der GA 22-37 VSDS keinen Kompressorraum. Er kann in der Produktionshalle installiert werden und nimmt nur wenig Platz in Anspruch. Zudem wurde der Kompressor mit der Fernüberwachung Smartlink ausgestattet.
Lückenloses Reporting
Mit dem smarten Service-Tool Boge connect lassen sich Druckluftsysteme analysieren und optimieren. Dabei hat der Anwender ständig alle Betriebsdaten im Blick: Das Tool erfasst, überwacht und visualisiert alle wichtigen Parameter und vereinfacht damit den administrativen Aufwand. Alle relevanten Daten sind in einer digitalen Maschinenakte hinterlegt. Die kontinuierliche Überwachung lässt jederzeit Rückschlüsse auf den Zustand der Maschine zu. Durch die Auswertung von Daten können Auffälligkeiten erkannt und Störungen frühzeitig behoben werden. Rechtzeitig und automatisch erinnert Boge connect an bevorstehende Wartungen. Die Daten sind in Echtzeit von überall abrufbar und auf sämtlichen mobilen Endgeräten verfügbar. Über eine Vielzahl von Schnittstellen lassen sich auch ältere Modelle und sogar Fremdfabrikate sowie zahlreiche Komponenten anbinden. Die überarbeitete Version verfügt über neue Interface-Module 2.0 für den Anschluss von Kompressoren und Zubehörteilen. Mit Boge connect lässt sich die Performance weiter steigern, denn das lückenlose Reporting über den gesamten Lebenszyklus hinweg sorgt für niedrigere Betriebskosten sowie höhere Effizienz.
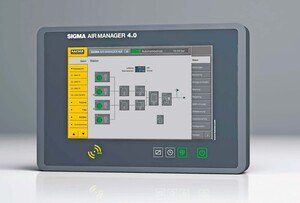
Optimale Leistungen
Kaeser hat den Schraubenkompressoren der CSD/CSDX-Baureihe zahlreiche Features spendiert, womit diese noch effizienter und energiekostensparender arbeiten. Die Baureihe punktet mit bestmöglichen Energieeffizienzklassen im Antrieb (bei Drehzahlregelung mit IE5, Festdrehzahl mit IE4). Herzstück aller Kompressoren ist ein speziell für diesen Leistungsbereich entwickelter Kompressorblock mit dem strömungstechnisch optimierten Sigma Profil. Durch diese sowie weitere Optimierungen wie etwa den drehzahlgeregelten Lüftermotoren, konnte die Energieeffizienz der Kompressoranlage deutlich verbessert werden, der Energieverbrauch deutlich gesenkt. Mit Motorleistungen von 45 bis 110 Kilowatt deckt die Baureihe Liefermengen von 8,4 bis rund 19,4 Kubikmeter pro Minute ab und ist für Drücke bis 15 bar ausgelegt. Insbesondere bei niedrigen Drücken können noch höhere Liefermengen realisiert werden. Kaeser will mit diesen Maßnahmen die Energiekosten senken und die CO2-Bilanz verbessern.