Komplexe Tiefbauprojekte
Am Spezialtiefbau führt kein Weg vorbei

Bauvorhaben benötigen üblicherweise ein solides Fundament – und zwar präzise abgestimmt auf die jeweilige Bodenbeschaffenheit und den vorgesehenen Verwendungszweck. Gerade bei größeren Bauvorhaben oder auch Infrastrukturprojekten sind dabei Speziallösungen gefragt. Wenig Wunder also, dass sich der Spezialtiefbau in den letzten Jahrzehnten zu einem essenziellen Bestandteil der Bauindustrie entwickelt hat. Gerade bei der Realisierung anspruchsvoller Bauprojekte in urbanen Umgebungen und bei der Bewältigung der wachsenden infrastrukturellen Herausforderungen spielt diese hochspezialisierte Disziplin des Bauwesens eine entscheidende Rolle.
Ganz egal, ob es um Baugrubensicherung, Hangsicherung, Tiefgründung oder auch Dichtwände für Hochwasserschutzprojekte und Bodenverbesserungen geht, am Spezialtiefbau führt heute kein Weg vorbei. Die Technik entwickelt sich dementsprechend kontinuierlich weiter. Etwa im Bereich der Bohrtechniken. Moderne Bohrmaschinen sind heute in der Lage, selbst in den härtesten Bodentypen zu arbeiten, wodurch die Effizienz und Präzision von Bauprojekten erheblich verbessert werden. Die Einführung von computergesteuerten Bohrsystemen ermöglicht es Ingenieuren zudem, die Tiefe, Neigung und Richtung der Bohrungen genau zu kontrollieren, was bei Projekten wie dem Bau von Tunneln und Fundamenten von Hochhäusern von entscheidender Bedeutung ist. Darüber hinaus nutzen einige Unternehmen auch innovative Technologien wie Schall- und Vibrationssensoren, um potenzielle Auswirkungen auf die Umgebung zu minimieren.
Das Schweizer Unternehmen Kibag erstellt beispielsweise für die Schifffahrtsgesellschaft am Vierwaldstättersee neue Anlegepfähle. Dafür wurde von Kibag zum ersten Mal ein Bohrgerät aus der „LB“-Serie von Liebherr genutzt. „Das Problem ist, dass wir hier nicht rammen können,“ erklärt Markus Waldis, seines Zeichens Polier bei Kibag. „Der Boden ist zu hart. Daher müssen wir die Pfähle bohren und dann betonieren.“
Herausforderung schwimmend bohren
In Seelisberg, an der Südseite des Vierwaldstättersees, bohrt das Team daher von einem Ponton aus mit dem Bohrgerät LB 30 die Pfähle – von der Wasseroberfläche abwärts rund zwölf Meter bei einem Durchmesser von 1.300 Millimetern. „Nach einer Wassertiefe von drei Metern kommt ein Steinsegment, und danach muss mindestens sechs Meter in den Felsen gebohrt werden.
Genau dieser Fels wurde zum Härtetest für das Baustellenpersonal und besonders für das neue LB 30. „Der Stein ist einfach pickelhart. Die ganze Maschine vibriert“, betont Waldis die extremen Herausforderungen. Erschwerend komme hinzu, dass mit dem Bohrgerät vom Ponton aus nicht genügend Druck ausgeübt werden kann. „Ansonsten heben wir nur den Ponton. Den müssen wir sehr gut sichern, damit er beim Bohren hält.“
„Da der Grund sehr hart ist, müssen wir die Spitze der Bohrschnecke sehr oft wechseln, um in den Felsen bohren zu können“, erläutert Gianluca Diaco, der seit 14 Jahren Gerätefahrer bei Kibag ist und im Zuge des Projekts zum ersten Mal auf einer Wasserbaustelle arbeitete. Trotz der schwierigen Voraussetzungen zeigt er sich vom Liebherr-Bohrgerät überzeugt. „Es ist sehr stark, kompakt und schnell in den Bewegungen. Man kann alles damit machen.“ Waldis ergänzt: „Das Gerät läuft einwandfrei – tipptopp. Es muss große Vibrationen aushalten. Es ist ein großer Härtetest für die Maschine. Aber bis jetzt meistert sie es wunderbar.“
Nachdem die Wasserbauspezialisten von Kibag die Außenrohre betoniert haben, kommt der Anlegepfahl für die Schiffe hinein. Ein Gummi zwischen Außenrohr und Pfahl sorge dabei dafür, dass sich der Pfahl etwas bewegen kann und nicht zu starr ist, wenn Schiffe anlegen. Damit sich der Anlegepfahl nicht drehen kann, muss dieser unter Wasser von einem Taucher gesichert werden.
Um das Bohrgerät überhaupt auf die Baustelle zu bringen, sei das Team von Kibag mit dem Ponton rund sechs Stunden über den See gefahren. Die Achereggbrücke im Südwesten des Vierwaldstättersees war dabei eine erste Herausforderung, wie Waldis erklärt. „Wir mussten auf die Höhe achten und konnten das Bohrgerät erst nach der Brücke, also erst auf See, aufstellen. Unser Ponton ist relativ groß – rund 18 Meter breit und 40 Meter lang –, und wir haben viel Gewicht darauf. Das hat alles sehr erschwert.“
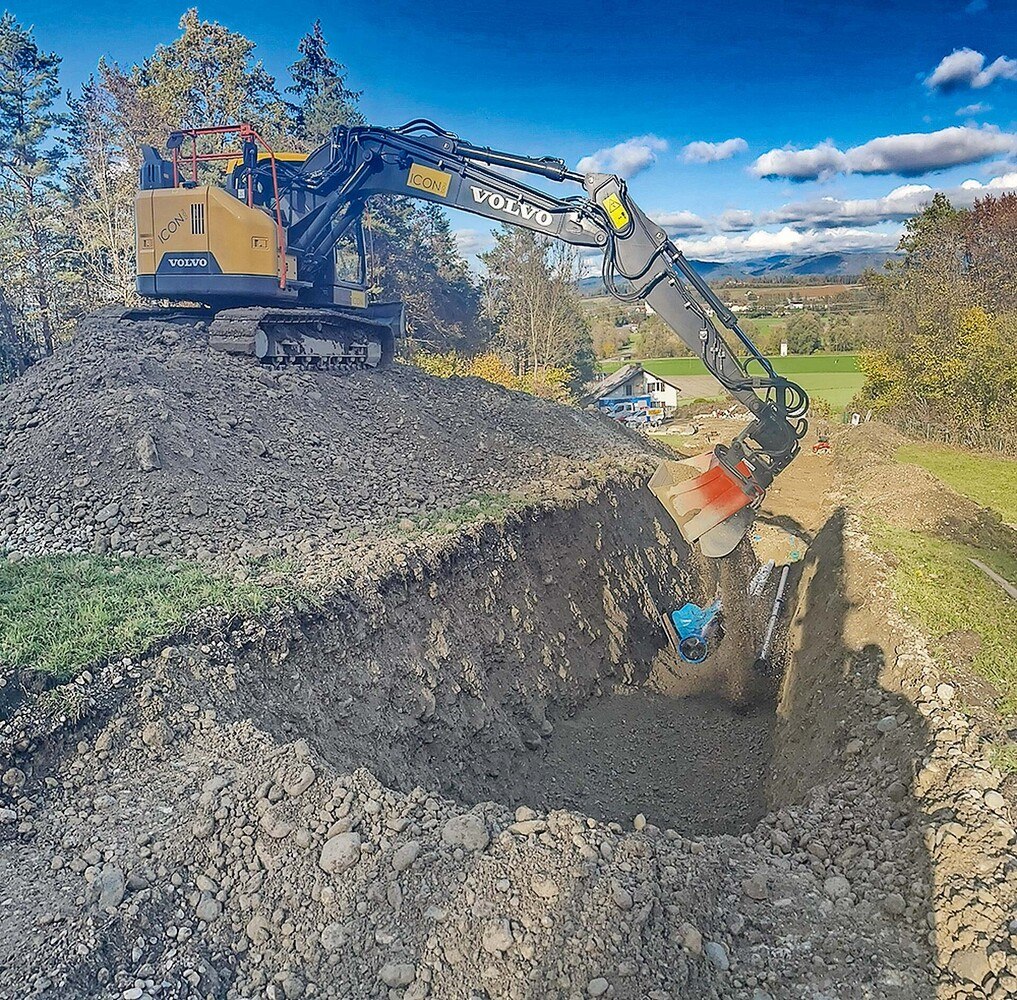
Steiles Baugebiet
Auch die Marktgemeinde Grafenstein stellte den Spezialtiefbau vor große Herausforderungen. Die Gemeinde grenzt im Osten an die Kärntner Landeshauptstadt Klagenfurt und gilt als attraktive Zuzugsgemeinde. Mit Beginn Mitte Oktober 2022 wurde die alte und sanierungsbedürftige Ableitung vom Hochbehälter in Grafenstein ausgetauscht. Im Zuge der Sanierung wurden insgesamt drei Leitungen (einmal DN 300 und zweimal DN 150) auf einer Länge von insgesamt 300 Laufmeter ausgetauscht. Zudem wurden auch Arbeiten im beziehungsweise am Hochbehälter durchgeführt.
Dabei wurden duktile Gussrohre der Tiroler Rohre GmbH (TRM) in DN 300 und DN 150 VRS-T mit Pur-LL-Beschichtung und mit dem besonderen Korrosionsschutz ZMU Austria eingesetzt. Zusätzlich kommen im Armaturenbereich Produkte von Hawle zum Einsatz. Eine besondere Schwierigkeit bei dem Projekt sei die große Steilheit im Baugebiet gewesen, wie die Projektbeteiligten betonten.
Sechs Jahre Bauzeit
Die Errichtergesellschaft BBT SE hat indes den Zuschlag für den Bau der Tunnelstrecke Pfons–Brenner an eine Arbeitsgemeinschaft von Porr Bau GmbH, der Marti GmbH und Marti Tunnel AG erteilt. „Wir freuen uns, mit unserem Partner Marti dieses Jahrhundertprojekt in Angriff nehmen zu können“, erklärt Porr-CEO Karl-Heinz Strauss. „Der Brenner Basistunnel ist eine wichtige Antwort auf das Kernthema Mobilität, dem sich Europa widmen muss.“
Aufgrund ihrer weitreichenden Kompetenzen im Tunnelbau konnte Porr laut Strauss bei der Auftragsvergabe mit dem besten Angebot überzeugen. „Wir haben unser Team neu aufgestellt und werden diese Teilstrecke nun zügig abwickeln. Der Brenner-Basistunnel soll als Verbindung zwischen Österreich und Italien seine Schlüsselrolle im europäischen Verkehrsnetz so schnell wie möglich einnehmen.“
Der Bau der Teilstrecke Pfons–Brenner (Baulos H53) werde rund sechs Jahre in Anspruch nehmen, der Auftragsumfang umfasst zwei eingleisige Haupttunnelröhren mit einer Gesamtlänge von insgesamt 25,2 km. Die Arge Porr-Marti setze dabei sowohl zwei Tunnelbohrmaschinen als auch den Sprengvortrieb ein. Jede der Tunnelbohrmaschinen mit einem Ausbruchdurchmesser von 10,37 m könne dabei eine Strecke von bis zu 30 m pro Tag zurücklegen. Zusätzlich zu den Hauptröhren sind weitere rund 3,6 km an Erkundungs- beziehungsweise Querschlagstunnelstrecken geplant.
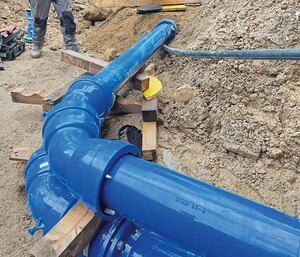
Herausforderung Nachhaltigkeit
Auch die zunehmende Nachfrage nach nachhaltigen Bauprojekten beeinflusst den Spezialtiefbau. So arbeiten Ingenieure mittlerweile verstärkt daran, umweltfreundliche Materialien zu verwenden und den Energieverbrauch während des Bauprozesses zu reduzieren. Dies beinhaltet auch die Entwicklung von Techniken zur Minimierung von Bodenverunreinigungen und zur Wiederverwendung von Baustoffen, um die Umweltauswirkungen zu minimieren. Ein Beispiel hierfür ist die Verwendung von Geotextilien und Geokunststoffen, um Bodenerosion zu verhindern und die Tragfähigkeit von Böden zu erhöhen.
Der Spezialtiefbau profitiert dabei auch erheblich von der Digitalisierung und dem Einsatz von Building Information Modeling (BIM). Durch die Erstellung präziser digitaler Modelle können Ingenieure Bauprojekte genauer planen und simulieren, was zu effizienteren Bauabläufen und einer besseren Ressourcennutzung führt. Die Integration von Sensortechnologie ermöglicht zudem eine kontinuierliche Überwachung der Baustellenbedingungen und trägt zur Sicherheit der Arbeiter bei. Die Daten, die während des Bauprozesses gesammelt werden, können auch für die Wartung und Instandhaltung der Bauwerke genutzt werden, was deren Lebensdauer erhöht.
Trotz der Fortschritte gibt es natürlich auch weiterhin diverse Herausforderungen im Spezialtiefbau. Eine der größten Herausforderungen dabei ist beispielsweise die Bewältigung komplexer Bodenverhältnisse, die von Projekt zu Projekt variieren können. Die Entwicklung neuer Bodenverbesserungstechniken, wie die Injektion von Bodenverfestigern oder die Anwendung von Mikropfählen, sowie die Anpassung von Maschinen an unterschiedliche Bodenbedingungen sind dementsprechend von großer Bedeutung.
Auch die steigenden Kosten für Rohstoffe und die Notwendigkeit, strengere Umweltauflagen einzuhalten, erhöhen den Druck auf Bauprojekte im Spezialtiefbau. Ingenieure und Auftragnehmer sind dadurch verstärkt gefordert, innovative Lösungen zu finden, um Budgets einzuhalten und dennoch höchste Qualitätsstandards zu erfüllen. Die Zusammenarbeit zwischen öffentlichen Institutionen und privaten Unternehmen wird dabei immer wichtiger, um die Finanzierung und Durchführung großer Infrastrukturprojekte zu gewährleisten.
Forschungsprojekt
Zustandsbewertung von geankerten Konstruktionen
Geankerte Konstruktionen sind ein wesentlicher Bestandteil der Geotechnik, die vor allem als Baugrubensicherung, zur Herstellung von Stützbauwerken und für weitere Hangsicherungsmaßnahmen eingesetzt werden. Aufgrund der technischen, ökonomischen und nicht zuletzt ökologischen Vorteile, die mit der Errichtung derartiger Bauwerke einhergehen, werden diese insbesondere im Nahbereich von Infrastrukturanlagen ausgeführt. Trotz aller Vorteile stellt die Verankerung mit metallischen Zuggliedern im Untergrund allerdings auch eine erhebliche Herausforderung für die Ingenieur*innen, die ausführenden sowie die erhaltenden Unternehmungen dar. Da die Bemessungslebensdauer mitunter bis zu hundert Jahre beträgt, bestehen enorme Anforderungen an die Dauerhaftigkeit von geankerten Konstruktionen. Inspektions- und Prüftätigkeiten an Bestandsbauwerken lassen hier nicht selten einen vermehrten Korrosionsangriff an den Zugelementen erkennen, welcher neben der optischen Beeinträchtigung auch eine sicherheitsrelevante Auswirkung – und somit eine Abnahme der Tragfähigkeit –nach sich zieht. Um den Erhaltungszustand des Bauwerks zu beurteilen und damit auch die Sicherheit zu gewährleisten, ist eine genaue und zuverlässige Erfassung der Konstruktion, einschließlich der Zugelemente, von größter Bedeutung. Neben der visuellen Begutachtung, der messtechnischen Überwachung sowie Ankerabhebekontrollen stehen aktuell jedoch nur unzureichende Methoden zur präzisen Erfassung sicherheitsrelevanter Einflussgrößen zur Verfügung.
Diesem Themenbereich hat sich daher das Forschungsprojekt Safety and Risk of Anchored Structures (SaRAS) angenommen, mit dem Ziel, neue und innovative Methoden zur Zustandsbewertung von geankerten Konstruktionen zu entwickeln und diese auch in der Praxis zu etablieren. Im Rahmen des Projekts wurden die bekannten Schadensbilder und Mängel an derartigen Konstruktionen in Zusammenarbeit mit Bauwerkserhalten und Ingenieurbüros aufbereitet, ergänzt durch die Aufnahme und Erfassung einiger ausgewählter Bauwerke. Die Ergebnisse sollen dabei in eine bestehende, öffentlich zugängliche Datenbank zu Ankersystemen einfließen, die eine Grundlage für die Zustandserfassung geankerter Konstruktionen bieten wird. Da die Qualität der Erfassung auch stark von der häufig unzureichenden Bauwerksdokumentation abhängt, wurde auch eine Methode zur Erfassung nicht einsehbarer Kennwerte (also etwa der Länge Freispiel- und Haftstrecke sowie Vorspannkraft) durch die dynamische Anregung der Bauteilkomponenten untersucht.
Weitere Infos finden Sie hier.
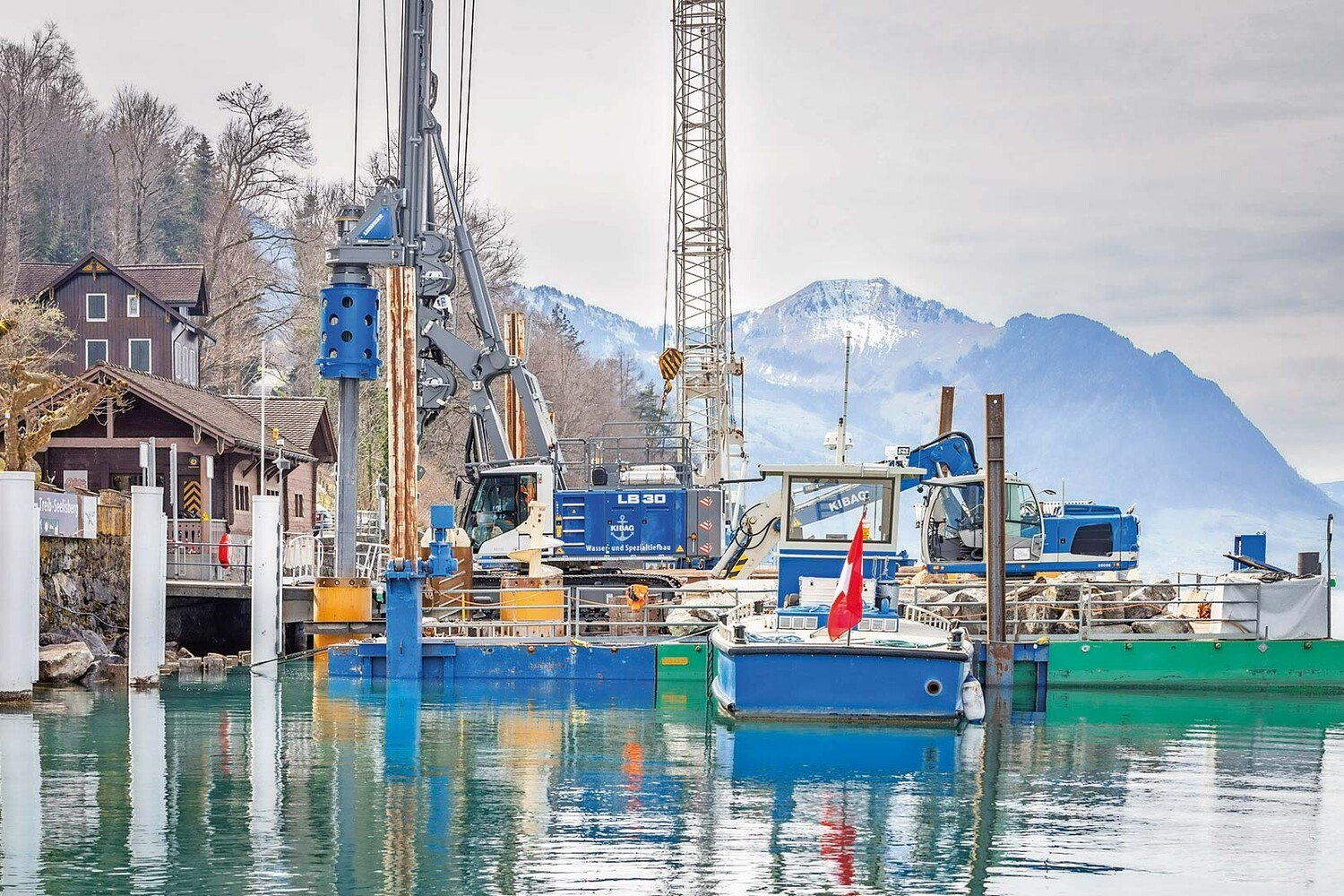
Liebherr
Produktportfolio um Unplugged-Modelle erweitert
Liebherr erweiterte vor einiger Zeit sein Engagement im Bereich der alternativen Antriebe und dehnte das Konzept auf weitere Produktbereiche aus. Mittlerweile bilden Raupenkrane, Ramm- und Bohrgeräte die elektrifizierte „Unplugged“-Serie. Ein besonderes Merkmal der batteriebetriebenen Unplugged-Geräte ist dabei „Zero Emission“, wie der Hersteller betont. Die Geräte würden einerseits keine Abgase verursachen und seien andererseits sehr leise. Damit würden sie besonders in lärmempfindlichen Regionen großen Anklang bei Baustellenpersonal und Anwohnern finden. Das Konzept werde unter anderem in London, Paris und Oslo bereits erfolgreich eingesetzt.
Das Laden der Batterien erfolge dabei über herkömmlichen Baustellenstrom. Während des Ladevorgangs könne der Betrieb wie gewohnt fortgesetzt werden. Um in den Akkubetrieb zu gelangen, müsse nur „der Stecker gezogen“ werden, so der Hersteller. Die Leistung und das Anwendungsspektrum würden aber – egal ob angesteckt oder „unplugged“ – unverändert bleiben, wie das Unternehmen verspricht.
Alle Modelle seien sowohl als konventionelle als auch batteriebetriebene Version erhältlich und hätten identische Leistungsdaten. Etwa die Rammen „LRH 100.1 unplugged“ und „LRH 200 unplugged“. Ein Batteriepaket mit 200 kWh sorge dafür, dass die Unplugged-Modelle im durchschnittlichen Rammeinsatz vier bis fünf Stunden im Batteriemodus betrieben werden könnten. Optional könne auch auf 400 kWh für acht bis zehn Stunden Betrieb aufgerüstet werden.
Das neue Konzept des LRH 200 erweitere dabei das Anwendungsspektrum und mache es noch vielseitiger im Einsatz. Neben dem Rammen könne das Gerät für Bohrarbeiten mit Endlosschnecke, Vollverdrängerausrüstung oder Imlochhammer sowie zum Nassmischen eingesetzt werden. Ein Drehmoment von 250 kNm sorge dabei für die nötige Kraft.
Ausgerüstet mit dem hydraulischen Hammer „H 6“ könnten Pfähle bis zu einer Länge von 24,5 Meter und einem Gewicht von 16 Tonnen aufgezogen werden. Das Gerät zeichne sich zudem durch einen großen Arbeitsbereich aus. Eine Ausladung bis zu 8,7 Meter habe überdies den Vorteil, dass die Maschine beim Arbeiten nicht ständig umgesetzt werden müsse.
Die Bohrgeräte „LB 25“ und „LB 30“ wiederum hätten sich als konventionelle Version bereits über Jahre bewährt. Die neuen batteriebetriebenen Unplugged-Versionen seien daher in Bezug auf Einsatzmöglichkeiten, Gewicht oder Transport identisch, hätten jedoch den zusätzlichen Vorteil von „Zero Emission“. Die Bohrgeräte könnten für alle gängigen Anwendungen im Bereich Spezialtiefbau eingesetzt werden.
Durch die optionale Verlängerung der Bohrachse könnten die Maschinen für Bohrdurchmesser bis zu 3,4 Meter eingesetzt werden. Die optionale Heckabstützung und das neue Design des modularen Heckballastes würden für mehr Stabilität und eine längere Lebensdauer sorgen. Beide Geräte seien neben der Standardkonfiguration mit einer Gesamthöhe von 14,1 Meter als Low Head oder nur 7,7 Meter als Ultra Low Head erhältlich. Für den Batteriebetrieb müsse – wie auch bei den Rammen – das Ladekabel nur ausgesteckt und für einen unbegrenzten Einsatz wieder an die Stromversorgung der Baustelle angeschlossen werden.
Auch im Bereich der Krane wurde das Portfolio um die Modelle „LR 1130.1 unplugged“ und „LR 1160.1 unplugged“ ergänzt. Auch hier weise der elektrohydraulische Antrieb dieselben Leistungsdaten wie bei den konventionellen Versionen auf. Die Kapazität der Batterie sei dabei für einen durchschnittlichen Hebebetrieb von acht Stunden ausgelegt. Die Batterie könne in nur 2,5 bis 4,5 Stunden wieder aufgeladen werden, optional könne die Leistung mittels zusätzlicher Batterien um 20 bis 60 Prozent erhöht werden.